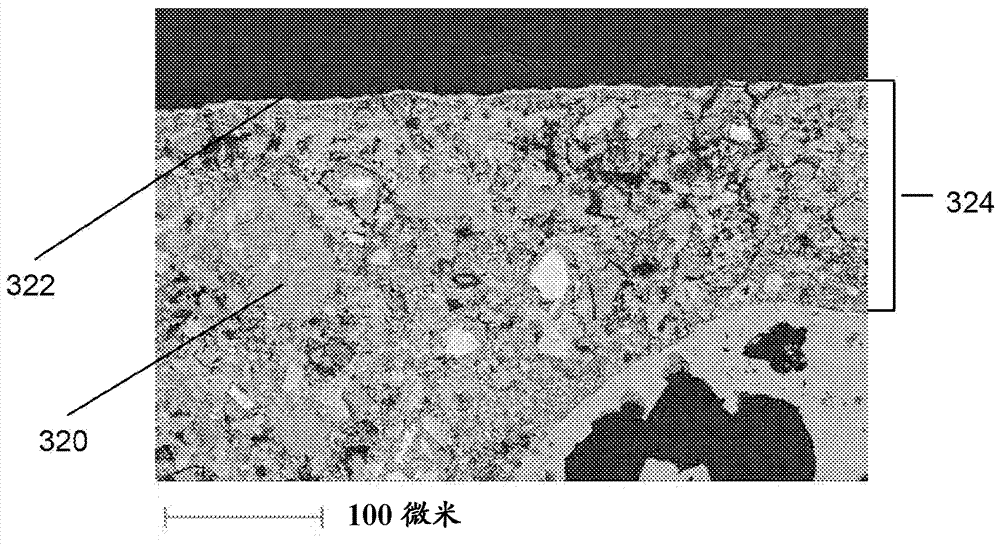
用于鑄塑鈦和鋁化鈦合金的模具和表面涂層組合物以及方法
背景技術:對于可靠性、重量、功率、經濟和操作使用壽命而言,現代燃氣輪機或燃氣渦輪必須滿足最高要求。在開發這樣的渦輪中,除了別的以外,材料選擇、對新的合適的材料的搜尋以及對新的生產方法的搜尋在滿足標準和滿足該要求中起到重要的作用。用于燃氣輪機的材料可包括鈦合金、鎳合金(也稱為超合金)和高強度鋼。對于飛機發動機,鈦合金通常用于壓縮機零件,鎳合金適用于飛機發動機的熱零件,而高強度鋼例如用于壓縮機殼體和渦輪殼體。高度載荷或受應力的燃氣輪機部件,例如用于壓縮機的部件,例如通常為鍛造的零件。另一方面,用于渦輪的部件,通常體現為熔模鑄造零件。雖然熔模鑄造不是新的工藝,但是隨著更加錯綜復雜零件的要求提高,熔模鑄造市場持續增長。由于對高品質精密鑄件的高要求,持續需要開發新的方式來更加快、有效、廉價地制備具有更高品質的熔模鑄件。用于鑄塑珠寶和牙齒假體行業的由熔融二氧化硅、方石英、石膏等組成的常規的熔模鑄造模具化合物(investmentmoldcompound)通常不適于鑄塑反應性合金,例如鈦合金。一個原因是因為在模塑鈦和熔模鑄造模具之間存在反應。需要一種與鈦和鋁化鈦合金不顯著反應的簡單的熔模鑄造模具。以前已采取使用陶瓷外殼模具用于鈦合金鑄件的方法。在先前實例中,為了降低常規的熔模鑄造模具化合物的限制,已開發若干另外的模具材料。例如,開發了氧化膨脹類型的熔模鑄造化合物,其中氧化鎂或氧化鋯用作主要成分,并且將金屬鋯加入到主要組成中,以補償由于鑄塑金屬的凝固引起的收縮。因此,還需要簡單和可靠的熔模鑄造方法,其允許從不與金屬或金屬合金顯著反應的熔模鑄造模具容易提取近凈形狀(near-net-shape)金屬或金屬合金。發明概述本公開的多方面提供克服常規技術的限制的鑄塑模具組合物、鑄塑方法和鑄塑制品。雖然本公開的一些方面可涉及制造航天行業的部件,例如,發動機渦輪葉片,但是本公開的多方面可用于在任何行業中制造任何部件,特別是,含鈦和/或鈦合金的那些部件。本公開的一方面為一種用于鑄塑含鈦制品的模具,所述模具包含:包含單鋁酸鈣、二鋁酸鈣和鈣鋁石的鋁酸鈣水泥,其中在模具的主體和模具腔之間,所述模具具有約10微米-約250微米的內在表面涂層。在一個實施方案中,表面涂層為連續的內在表面涂層。在一個實施方案中,所述模具還包含二氧化硅,例如,膠態二氧化硅。在一個實例中,模具包含模具的主體和內在表面涂層,其中模具的主體和內在表面涂層具有不同的組成,并且內在表面涂層包含粒度小于約50微米的鋁酸鈣。在另一個實施方案中,模具包含模具的主體和內在表面涂層,其中模具的主體和內在表面涂層具有不同的組成,并且其中所述模具的主體包含大于約50微米的氧化鋁顆粒。在另一個實例中,模具包含模具的主體和內在表面涂層,其中所述模具的主體包含大于約50微米的氧化鋁顆粒,并且所述內在表面涂層包含尺寸小于約50微米的鋁酸鈣顆粒。在某些實施方案中,比起模具的主體,內在表面涂層中單鋁酸鈣的重量分數多至少20%。在一個實施方案中,比起模具的主體,內在表面涂層中氧化鋁的重量分數少至少20%。在另一個實施方案中,比起模具的主體,內在表面涂層中鋁酸鈣的重量分數多至少20%,氧化鋁的重量分數少至少20%,并且鈣鋁石的重量分數少至少50%。在一個實例中,在內在表面涂層中單鋁酸鈣的重量分數多于0.60,并且鈣鋁石的重量分數小于0.10。在一個實施方案中,在模具的主體中單鋁酸鈣的重量分數為約0.05-0.95,而在內在表面涂層中單鋁酸鈣的重量分數為約0.10-0.90。在另一個實施方案中,在模具的主體中二鋁酸鈣的重量分數為約0.05-約0.80,而在內在表面涂層中二鋁酸鈣的重量分數為約0.05-0.90。在又一個實施方案中,在模具組合物的主體中鈣鋁石的重量分數為約0.01-約0.30,而在內在表面涂層中鈣鋁石的重量分數為約0.001-0.05。在一個具體的實施方案中,在模具的主體中單鋁酸鈣的重量分數為約0.05-0.95,而在內在表面涂層中單鋁酸鈣的重量分數為約0.1-0.90;在模具的主體中二鋁酸鈣的重量分數為約0.05-約0.80,而在內在表面涂層中二鋁酸鈣的重量分數為約0.05-0.90;并且其中在模具組合物的主體中鈣鋁石的重量分數為約0.01-約0.30,而在內在表面涂層中鈣鋁石的重量分數為約0.001-0.05。在一個實例中,在模具的主體中,模具還包含外部尺寸小于約500微米的氧化鋁顆粒。在一個實例中,氧化鋁顆粒占用于制備模具的組合物的約40重量%-約68重量%。這些氧化鋁顆粒可為空心的。在另一個實施方案中,鋁酸鈣水泥占用于制備模具的組合物的多于30重量%。在一個實施方案中,模具還包含模具組合物的多于約10重量%并且小于約50重量%的氧化鈣。在一個實例中,模具還包含氧化鋁顆粒、氧化鎂顆粒、氧化鈣顆粒、氧化鋯顆粒、氧化鈦顆粒、氧化硅顆粒,或它們的組合物。在一個實例中,在用于制備模具的初始鋁酸鈣-液體水泥混合物中固體的重量百分比為約71%-約78%。在另一個實例中,在用于制備模具的具有大規格氧化鋁的最終鋁酸鈣-液體水泥混合物中固體的重量百分比為約75%-約90%。本公開的一方面為在模具中形成的含鈦制品。在一個實例中,制品包含含鋁化鈦的渦輪葉片。在一方面,本公開為本文描述的模具,其中所述模具形成含鈦制品。在一個相關的實施方案中,含鈦制品包含含鋁化鈦的渦輪葉片。本公開的一方面為用于鑄塑含鈦制品的模具的表面涂層組合物,所述表面涂層組合物包含:單鋁酸鈣、二鋁酸鈣和鈣鋁石,其中所述表面涂層組合物為內在表面涂層,為約10微米-約250微米厚,并且位于模具的主體與朝向模具腔的模具的表面之間。在一個實例中,表面涂層包含粒度小于約50微米的鋁酸鈣。在一個實施方案中,表面涂層組合物還包含二氧化硅,例如,膠態二氧化硅。在一個實施方案中,比起模具的主體,內在表面涂層中鋁酸鈣的重量分數多至少20%,氧化鋁的重量分數少至少20%,并且鈣鋁石的重量分數少至少50%。在一個實例中,在內在表面涂層中單鋁酸鈣的重量分數多于0.60,并且鈣鋁石的重量分數小于0.10。在一個實施方案中,在內在表面涂層中單鋁酸鈣的重量分數為0.10-0.90;在內在表面涂層中二鋁酸鈣的重量分數為0.05-0.90;并且在內在表面涂層中鈣鋁石的重量分數為0.001-0.05。本公開的一方面為一種用于形成用于鑄塑含鈦制品的鑄塑模具的方法,所述方法包括:使鋁酸鈣與液體組合,以生產鋁酸鈣的漿料,其中在初始鋁酸鈣/液體混合物中固體的重量百分比為約70%-約80%,并且漿料的粘度為約10-約250厘泊;將氧化物顆粒加入到漿料中,使得在具有大規格(大于50微米)氧化物顆粒的最終的鋁酸鈣/液體混合物中固體的重量百分比為約75%-約90%;將漿料引入到含有短效圖案(fugitivepattern)的模具腔中;和允許漿料在模具腔中固化,以形成含鈦制品的模具。本公開的一方面為一種用于鈦和鈦合金的鑄塑方法,所述方法包括:得到包含鋁酸鈣和氧化鋁的熔模鑄造模具組合物,其中將鋁酸鈣與液體組合,以生產鋁酸鈣的漿料,并且其中在具有大規格氧化鋁的最終的鋁酸鈣/液體混合物中固體的重量百分比為約75%-約90%,并且其中所得到的模具具有內在表面涂層;將所述熔模鑄造模具組合物倒入含有短效圖案的容器中;固化所述熔模鑄造模具組合物;從模具中除去短效圖案;焙燒(firing)模具;將模具預熱至模具鑄塑溫度;將熔融的鈦或鈦合金倒入已加熱的模具中;使熔融的鈦或鈦合金凝固,并且形成凝固的鈦或鈦合金鑄件;和從模具中移出所述凝固的鈦或鈦合金鑄件。在一個實施方案中,要求保護通過本文教導的鑄塑方法制備的鈦或鈦合金制品。本公開的一方面為用于鑄塑含鈦制品的模具組合物,所述組合物包含:包含單鋁酸鈣、二鋁酸鈣和鈣鋁石的鋁酸鈣水泥。在一個實施方案中,模具組合物還包含空心氧化鋁顆粒。本公開的另一方面為含鋁酸鈣的含鈦制品鑄塑模具組合物。例如,本公開的一方面可獨特地適于提供模具組合物,所述模具組合物用于用來鑄塑含鈦和/或含鈦合金的制品或部件例如含鈦渦輪葉片的模具。結合附圖,由本公開的多個方面的以下詳細說明,本公開的這些和其它方面、特征和優點將變得顯而易見。附圖概述在說明書的結論處,在權利要求書中特別指出和清楚地要求保護視作本發明的主題。結合附圖,由本發明的多方面的以下詳細說明,本公開的前述和其它特征和優點將變得容易理解,附圖中:圖1a和1b顯示在高溫焙燒后模具微觀結構的一個實施例,其具有在1000℃下焙燒的模具的橫截面的反向散射電子成像掃描電子顯微鏡圖像,其中圖1a表示存在的氧化鋁顆粒,圖1b表示鋁酸鈣水泥。圖1a還顯示模具微觀結構,顯示模具的主體,內在表面涂層的位置,和模具/模具腔的內表面。圖2a和圖2b顯示在高溫焙燒后模具微觀結構的一個實施例,其具有在1000℃下焙燒的模具的橫截面的反向散射電子成像掃描電子顯微鏡圖像,其中圖2a表示存在的鋁酸鈣水泥和微型(finescale)氧化鋁顆粒,圖2b表示氧化鋁顆粒。圖2b還顯示模具微觀結構,顯示模具的主體,內在表面涂層的位置,和模具/模具腔的內表面。圖3和4顯示在高溫焙燒后模具微觀結構的實施例,顯示氧化鋁和單鋁酸鈣,其中單鋁酸鈣與氧化鋁反應,以形成二鋁酸鈣,并且其中在一個實施例中,將模具焙燒,以使鈣鋁石含量最小化。圖5a顯示根據本公開的多方面的流程圖,說明一種用于形成用于鑄塑含鈦制品的鑄塑模具的方法。圖5b顯示根據本公開的多方面的流程圖,說明一種用于鈦和鈦合金的鑄塑方法。圖6顯示作為溫度的函數的模具主體的導熱性;將模具的導熱性與整體氧化鋁的導熱性(NIST數據)比較。圖7顯示具有表面涂層的模具的示意圖。圖7中的A)圖顯示具有例如約100微米厚的內在表面涂層的模具。示意性顯示內在表面涂層,其中還指示模具腔和鋁酸鈣模具位置。圖7中的B)圖顯示具有約100微米厚的外在表面涂層的模具。示意性顯示外在表面涂層,其中還指示模具腔和鋁酸鈣模具位置。發明詳述本公開主要涉及模具組合物和模具制備方法和由模具鑄塑的制品,更具體地,本公開涉及模具組合物和鑄塑含鈦制品的方法以及這樣模塑的含鈦制品。從鑄件應鑄塑為“近凈形狀”的角度來看,在熔模鑄造外殼模具中通過熔模鑄造鈦及其合金來制造基于鈦的部件造成問題。也就是,可將部件鑄塑為部件實質上最終期望的尺寸,并且需要很少或不需要最終的處理或機械加工。例如,一些常規的鑄件可僅需要化學研磨操作,以除去在鑄件上存在的任何α殼體(alphacase)。然而,在鑄件中位于α殼體下面的任何表面下的陶瓷包含物通常不能通過化學研磨操作除去,并且可能因模具表面涂層和模具中的任何反應性金屬(例如,反應性鋁化鈦)之間的反應而形成。本公開提供了一種用于鑄塑近凈形狀鈦和鋁化鈦部件(例如,渦輪葉片或機翼)的新的方法。本公開的實施方案提供用于熔模鑄造模具的物質的組合物和提供改進的鈦和鈦合金部件的鑄塑方法,所述部件例如用于航天、工業和海運行業。在一些方面,模具組合物提供這樣的模具,其含有在模具制備期間提供改進的模具強度和/或在鑄塑期間提供提高的對與鑄塑金屬反應的抗性的相。本公開的多方面的模具可能能夠在高壓下鑄塑,這是近凈形狀鑄塑方法期望的。已鑒定例如含有鋁酸鈣水泥和氧化鋁顆粒和優選的組成相的模具組合物,其提供具有改進的性質的鑄件。在一方面,模具的組成相包含單鋁酸鈣(CaAl2O4)。本發明人發現由于至少兩個原因而期望單鋁酸鈣。首先,本發明人理解,單鋁酸鈣促進在模具制備的初始階段期間在水泥顆粒之間的液壓結合(hydraulicbond)形成,認為該液壓結合在模具構造期間提供模具強度。第二,本發明人理解,單鋁酸鈣經歷非常低速率的與基于鈦和鋁化鈦的合金的反應。在某一實施方案中,向本公開的模具組合物(例如,鋁酸鈣水泥形式的熔模鑄造模具)提供單鋁酸鈣。在一方面,模具組合物包含鋁酸鈣水泥和氧化鋁(即,氧化鋁)的混合物。在本公開的一方面,在鑄塑期間,模具組合物提供與合金最小的反應,并且模具提供具有所需的組分性質的鑄件。鑄件的外部性質包括諸如形狀、幾何結構和表面光潔度等特征。鑄件的內部性質包括機械性質、微觀結構、低于規定尺寸并且在容許的限度內的缺陷(例如孔和內含物)。在一個實施方案中,在模具的主體和模具腔之間,模具含有連續的內在表面涂層。在一個相關的實施方案中,內在表面涂層為約50微米-約250微米。在某些情況下,表面涂層包含粒度小于約50微米的鋁酸鈣。模具組合物可使得模具的主體包含氧化鋁和大于約50微米的顆粒。在某一實施方案中,比起模具的主體,表面涂層具有較少的氧化鋁,并且其中比起模具的主體,表面涂層具有更多的鋁酸鈣。在初始鋁酸鈣-液體水泥混合物中固體的重量百分比以及在最終鋁酸鈣-液體水泥混合物中固體的重量百分比為本公開的特征。在一個實例中,在初始鋁酸鈣-液體水泥混合物中固體的重量百分比為約71%-約78%。在一個實例中,在初始鋁酸鈣-液體水泥混合物中固體的重量百分比為約70%-約80%。在另一個實例中,在具有大規格氧化鋁(>100微米)氧化鋁顆粒的最終鋁酸鈣-液體水泥混合物中固體的重量百分比為約75%-約90%。將初始鋁酸鈣水泥和微型(小于10微米)氧化鋁與水混合,以提供均勻和均質漿料;通過向初始漿料中加入大規格(大于100微米)氧化鋁并且混合2-15分鐘以獲得均勻混合物,而形成最終的模具混合物。本公開的一方面的模具組合物提供低成本鑄塑鋁化鈦(TiAl)渦輪葉片,例如,TiAl低壓渦輪葉片。模具組合物可提供鑄塑近凈形狀零件的能力,所述近凈形狀零件比起使用常規的外殼模具和重力鑄塑制備的零件,需要較少機械加工和/或處理。本文使用的表述“近凈形狀”意指制品的初始生產接近制品的最終(凈)形狀,降低進一步處理的需要,例如,廣泛的機械加工和表面精加工。本文使用的術語“渦輪葉片”是指蒸汽渦輪葉片和燃氣渦輪葉片二者。因此,本公開解決生產模具(例如,熔模鑄造模具)的挑戰,所述模具不與鈦和鋁化鈦合金顯著反應。此外,根據本公開的一些方面,模具的強度和穩定性允許高壓鑄塑方法,例如離心鑄塑。本公開的技術優點之一在于,在一方面,本公開可改進可例如由鋁酸鈣水泥和氧化鋁熔模鑄造模具產生的凈形狀鑄件的結構完整性。更高的強度(例如,更高的疲勞強度)允許制造更輕的部件。此外,具有更高的疲勞強度的部件可持續更久,因此具有較低的壽命周期成本。鑄塑模具組合物本公開的多方面提供用于可提供鈦和鈦合金的改進部件的熔模鑄造模具的物質的組合物。在本公開的一方面,可提供鋁酸鈣水泥形式的單鋁酸鈣。鋁酸鈣水泥可稱為“水泥”或“粘合劑”。在某些實施方案中,將鋁酸鈣水泥與氧化鋁顆粒混合,以提供可鑄塑的熔模鑄造模具混合物。在可鑄塑的模具混合物中鋁酸鈣水泥可大于約30重量%。在某些實施方案中,在可鑄塑的模具混合物中鋁酸鈣水泥為約30重量%-約60重量%。在可鑄塑的模具混合物(鑄塑模具組合物)中使用大于30重量%的鋁酸鈣水泥為本公開的特性。對適當的鋁酸鈣水泥化學性質和氧化鋁配方的選擇為模具性能的因素。在一方面,在模具組合物中可提供足夠量的氧化鈣,以使與鈦合金的反應最小化。在一方面,模具組合物,例如,熔模鑄造模具組合物,可包含鋁酸鈣水泥和氧化鋁顆粒的多相混合物。鋁酸鈣水泥可用作粘合劑,例如,鋁酸鈣水泥粘合劑可提供模具結構的主要骨骼結構。鋁酸鈣水泥可在模具中包含連續相并且在固化和鑄塑期間提供強度。模具組合物可由鋁酸鈣水泥和氧化鋁組成,也就是,鋁酸鈣水泥和氧化鋁可基本上構成模具組合物的僅有的組分,含有很少或不合其它組分。在一個實施方案中,本公開包括包含鋁酸鈣的含鈦制品鑄塑模具組合物。在另一個實施方案中,鑄塑模具組合物還包含氧化物顆粒,例如,空心氧化物顆粒。根據本公開的各方面,氧化物顆粒可為氧化鋁顆粒、氧化鎂顆粒、氧化鈣顆粒、氧化鋯顆粒、氧化鈦顆粒、氧化硅顆粒、它們的組合,或它們的組合物。在一個實施方案中,氧化物顆粒可為一種或多種不同的氧化物顆粒的組合。鑄塑模具組合物還可包含例如空心顆粒形式的氧化鋁,也就是,具有基本上由氧化物圍繞的空心核或基本上空心核的顆粒。這些空心氧化鋁顆粒可占氧化鋁的約99%,并且具有約10毫米[mm]或更少的外部尺寸,例如,寬度或直徑。在一個實施方案中,空心氧化鋁顆粒具有約1毫米[mm]或更少的外部尺寸,例如,寬度或直徑。在另一個實施方案中,氧化鋁包含可具有約10微米[μm]-約10,000微米范圍的外部尺寸的顆粒。在某些實施方案中,空心氧化物顆粒可包含空心氧化鋁球體(直徑通常大于100微米)。空心氧化鋁球體可摻入到鑄塑模具組合物中,并且空心球體可具有一定范圍的幾何形狀,例如,圓形顆粒或不規則的聚集體。在某些實施方案中,氧化鋁可包括圓形顆粒和空心球體二者。在一方面,發現這些幾何形狀提高熔模鑄造模具混合物的流動性。增強的流動性通常可改進由模具生產的最終鑄件的表面光潔度和表面特征的保真度或準確性。氧化鋁包含外部尺寸為約10微米-約10,000微米的顆粒。在某些實施方案中,氧化鋁包含外部尺寸(例如,直徑或寬度)小于約500微米的顆粒。氧化鋁可占鑄塑模具組合物的約0.5重量%-約80重量%。備選地,氧化鋁占鑄塑模具組合物的約40重量%-約60重量%。備選地,氧化鋁占鑄塑模具組合物的約40重量%-約68重量%。在一個實施方案中,鑄塑模具組合物還包含氧化鈣。氧化鈣可為鑄塑模具組合物的大于約10重量%并且小于約50重量%。最終的模具通常可具有小于2克/立方厘米的密度和大于500磅/平方英寸[psi]的強度。在一個實施方案中,氧化鈣為鑄塑模具組合物的大于約30重量%并且小于約50重量%。備選地,氧化鈣為鑄塑模具組合物的大于約25重量%并且小于約35重量%。本公開的一方面為一種用于鑄塑含鈦制品的模具,所述模具包含:包含單鋁酸鈣、二鋁酸鈣和鈣鋁石的鋁酸鈣水泥,其中在模具的主體和模具腔之間,模具具有約10微米-約250微米的內在表面涂層。在一個實施方案中,表面涂層為連續的內在表面涂層。在一個具體的實施方案中,本公開的鑄塑模具組合物包含鋁酸鈣水泥。鋁酸鈣水泥包含含有鈣和鋁的至少三個相或組分:單鋁酸鈣(CaAl2O4)、二鋁酸鈣(CaAl4O7)和鈣鋁石(Ca12Al14O33)。在內在表面涂層中單鋁酸鈣的重量分數可多于0.60,并且鈣鋁石的重量分數可小于0.10。在一個實施方案中,在模具的主體中單鋁酸鈣的重量分數為約0.05-0.95,而在內在表面涂層中單鋁酸鈣的重量分數為約0.1-0.90。在另一個實施方案中,在模具的主體中二鋁酸鈣的重量分數為約0.05-約0.80,而在內在表面涂層中二鋁酸鈣的重量分數為約0.05-0.90。在又一個實施方案中,在模具組合物的主體中鈣鋁石的重量分數為約0.01-約0.30,而在內在表面涂層中鈣鋁石的重量分數為約0.001-0.05。模具的主體和內在表面涂層的精確組成可不同。例如,在模具的主體中單鋁酸鈣的重量分數為約0.05-0.95,而在內在表面涂層中單鋁酸鈣的重量分數為約0.1-0.90;在模具的主體中二鋁酸鈣的重量分數為約0.05-約0.80,而在內在表面涂層中二鋁酸鈣的重量分數為約0.05-0.90;并且其中在模具組合物的主體中鈣鋁石的重量分數為約0.01-約0.30,而在內在表面涂層中鈣鋁石的重量分數為約0.001-0.05。在鋁酸鈣水泥中單鋁酸鈣的重量分數可多于約0.5,并且在鋁酸鈣水泥中鈣鋁石的重量分數可小于約0.15。在另一個實施方案中,鋁酸鈣水泥為鑄塑模具組合物的多于30重量%。在一個實施方案中,鋁酸鈣水泥的粒度為約50微米或更少。在一個實施方案中,適用于模具的主體的水泥的這些相的重量分數為0.05-0.95的單鋁酸鈣、0.05-0.80的二鋁酸鈣和0.01-0.30的鈣鋁石。在一個實施方案中,在模具的表面涂層中這些相的重量分數為0.1-0.90的單鋁酸鈣、0.05-0.90的二鋁酸鈣和0.001-0.05的鈣鋁石。在另一個實施方案中,在表面涂層中單鋁酸鈣的重量分數多于約0.6,并且鈣鋁石的重量分數小于約0.1。在一個實施方案中,在模具的主體的水泥中單鋁酸鈣的重量分數多于約0.5,并且鈣鋁石的重量分數小于約0.15。在一個實施方案中,鋁酸鈣水泥的粒度為約50微米或更少。出于三個原因,優選粒度小于50微米:首先,認為在模具混合和固化期間細粒度促進形成液壓結合;第二,了解在焙燒期間細粒度促進顆粒間燒結,這可提高模具強度;第三,認為細粒度改進在模具中生產的鑄塑制品的表面光潔度。鋁酸鈣水泥可作為粉末提供,并且可以其內在粉末形式或凝聚形式(例如作為噴霧干燥的附聚物)使用。鋁酸鈣水泥還可與微型(例如,尺寸小于10微米)氧化鋁預先混合。在高溫焙燒期間,由于燒結,認為微型氧化鋁提供強度提高。在某些情況下,還可與或不與含微型氧化鋁一起加入較大規格氧化鋁(也就是,尺寸大于10微米)。空心氧化鋁顆粒起至少兩個功能的作用:[1]它們在強度的最小降低的情況下降低模具的密度和重量;得到約500psi以上的強度水平,密度為約2g/cc以下;和[2]它們降低模具的彈性模量,并且在鑄塑后在模具和部件的冷卻期間有助于提供順應性。模具的提高的順應性和可壓碎性可降低在部件上的拉伸應力。鋁酸鈣水泥組合物用于本公開的多方面的鋁酸鈣水泥通常包含鈣和鋁的三個相或組分:單鋁酸鈣(CaAl2O4)、二鋁酸鈣(CaAl4O7)和鈣鋁石(Ca12Al14O33)。單鋁酸鈣為存在于鈣氧化鋁水泥中的液壓礦物質。單鋁酸鈣的水合有助于熔模鑄造模具的高的早期強度。鈣鋁石在水泥中是合乎需要的,因為由于快速形成液壓結合,鈣鋁石在模具固化的早期階段期間提供強度。然而,通常在鑄塑之間在模具的熱處理期間將鈣鋁石除去。在一方面,在水泥制造窯爐中焙燒之后,初始鋁酸鈣水泥配方通常不處于熱動力學平衡。然而,在模具制備和高溫焙燒之后,模具組合物朝向熱動力學穩定的構型移動,并且該穩定性對于隨后的鑄塑過程是有利的。在一個實施方案中,在水泥中單鋁酸鈣的重量分數大于0.5,并且鈣鋁石的重量分數小于0.15。將鈣鋁石摻入到模具的模具主體和表面涂層二者中,這是由于鈣鋁石為快速凝固鋁酸鈣,并且認為在固化的早期階段期間為模具的主體和表面涂層提供強度。固化可在低溫(例如,15℃-40℃溫度)下進行,因為短效蠟圖案對溫度敏感,并且在超過約35℃的熱暴露后失去其形狀和性質。優選在低于30℃的溫度下固化模具。鋁酸鈣水泥可通常通過將高純度氧化鋁與高純度氧化鈣或碳酸鈣混合而生產;通常在熔爐或窯爐中將化合物的混合物加熱至高溫,例如,1000-1500℃的溫度,讓其反應。將在窯爐中生產的所得到的產物(在本領域稱為水泥“熟料”),隨后壓碎、研磨和篩分,以生產具有優選的粒度的鋁酸鈣水泥。此外,設計和加工鋁酸鈣水泥,以具有最小量的雜質,例如,最小量的二氧化硅、鈉和其它堿金屬和鐵氧化物。在一方面,鋁酸鈣水泥的靶水平是Na2O、SiO2、Fe2O3和TiO2的總和小于約2重量%。在一個實施方案中,Na2O、SiO2、Fe2O3和TiO2的總和小于約0.05重量%。在本公開的一方面,提供鋁酸鈣水泥,其具有以氧化鋁(Al2O3)計超過35%重量的主體氧化鋁濃度和小于65%重量的氧化鈣。在一個相關的實施方案中,氧化鈣的該重量小于50%。在一個實例中,水泥的最大氧化鋁濃度可為約88%(例如,約12%CaO)。在一個實施方案中,鋁酸鈣水泥具有高純度并且含有至多70%氧化鋁。在鑄塑前,在焙燒的模具中,單鋁酸鈣的重量分數可最大化。可需要最小量的氧化鈣,以使在鑄塑合金和模具之間的反應最小化。如果在水泥中存在多于50%氧化鈣,這可產生諸如鈣鋁石和鋁酸三鈣等相,并且在鑄塑期間這些相不如單鋁酸鈣那么好地表現。氧化鈣的優選的范圍小于約50重量%并且大于約10重量%。如上所述,在模具的鋁酸鈣水泥/粘合劑中的三個相為單鋁酸鈣(CaAl2O4)、二鋁酸鈣(CaAl4O7)和鈣鋁石(Ca12Al14O33)。比起其它鋁酸鈣相,在產生表面涂層的水泥中的單鋁酸鈣具有三個優點:1)將單鋁酸鈣摻入到模具中,因為單鋁酸鈣具有快速凝固響應(雖然不如鈣鋁石快)并且認為在固化的早期階段期間為模具提供強度。快速產生模具強度提供鑄塑模具的尺寸穩定性,并且該特性改進最終鑄塑部件的尺寸一致性。2)對于正被鑄塑的鈦和鋁化鈦合金,單鋁酸鈣在化學上穩定。相對于二鋁酸鈣和具有較高氧化鋁活度的其它鋁酸鈣相,優選單鋁酸鈣;這些相與正被鑄塑的鈦和鋁化鈦合金具有更多的反應性。3)單鋁酸鈣和二鋁酸鈣為低膨脹相,并且理解為在固化、脫蠟和隨后的鑄塑期間,防止在模具中形成高水平的應力。單鋁酸鈣的熱膨脹行為與氧化鋁密切匹配。表面涂層在某些實施方案中,在模具的主體和模具腔之間,模具含有連續的內在表面涂層。設計模具以含有在模具制備期間提供改進的模具強度的相,并且設計連續的表面涂層,以在鑄塑期間提供對反應提高的抗性。模具能在高壓下鑄塑,這對于凈形狀鑄塑方法是期望的。已鑒定鑄塑模具組合物、表面涂層組合物和用于表面涂層和模具的主體的優選的組成相,其提供具有改進的性質的鑄件。表面涂層定義為與模具中的內表面或者模具腔相鄰的模具的區域。在一個實施方案中,表面涂層通常認為是約100微米厚的區域。為了更有效,表面涂層為連續的。在表面涂層后面并且遠離模具腔的區域稱為模具的主體。本公開的一方面為用于鑄塑含鈦制品的模具的表面涂層組合物,所述表面涂層組合物包含:單鋁酸鈣、二鋁酸鈣和鈣鋁石,其中表面涂層組合物為內在表面涂層,為約10微米-約250微米厚,并且位于模具的主體與朝向模具腔的模具的表面之間。在一個實例中,表面涂層包含粒度小于約50微米的鋁酸鈣。比起使用外在表面涂層,使用內在表面涂層具有優點。具體地,用于鑄塑的模具中的外在表面涂層(例如氧化釔或鋯石)在模具加工和鑄塑、尤其是高壓鑄塑期間可退化、裂紋和散裂。當模具填充熔融的金屬時,從外在表面涂層分離的表面涂層塊可被夾帶在鑄件中,并且陶瓷表面涂層變為在最終的零件中的包含物。包含物降低由鑄塑生產的部件的機械性能。在一個實施方案中,本公開提供用于熔模鑄造模具的內在表面涂層組合物以及主體模具組合物,它們共同可提供鈦和鈦合金的改進的鑄塑部件。在一個實施方案中,模具包含鋁酸鈣水泥和氧化鋁顆粒。在一個實例中,鋁酸鈣水泥起兩個功能的作用。首先,該水泥在通過除去短效圖案產生的模具的腔中產生原位表面涂層,第二,其用作在表面涂層后面的模具主體中的氧化鋁顆粒之間的粘合劑。在一個實施方案中,在模具中CaO的主體組成范圍為10-50重量%。在一個實施方案中,在表面涂層中CaO的組成為20-40重量%。在一個實施方案中,最終的模具具有小于2克/立方厘米的密度和大于500psi的強度。模具可包含模具的主體和內在表面涂層,其中模具的主體和內在表面涂層具有不同的組成,并且內在表面涂層包含粒度小于約50微米的鋁酸鈣。模具可包含模具的主體和內在表面涂層,其中模具的主體和內在表面涂層具有不同的組成,并且其中模具的主體包含大于約50微米的氧化鋁顆粒。在一個實例中,模具包含模具的主體和內在表面涂層,其中模具的主體包含大于約50微米的氧化鋁顆粒,而內在表面涂層包含尺寸小于約50微米的鋁酸鈣顆粒。在本公開中提供的凈形狀鑄塑方法允許零件可使用非破壞性方法更詳細且在更低的成本下檢查,所述非破壞性方法例如x-射線、超聲或渦流。降低與檢查輻射在過厚截面中的衰減和散射相關的困難。可能分辨較小的缺陷,這可提供具有改進的機械性能的零件。本公開提供了一種鑄塑模具組合物和鑄塑方法,其可提供鈦和鈦合金的改進部件。在一個實施方案中,使用鋁酸鈣水泥或粘合劑和氧化鋁顆粒構建模具。在一個實施方案中,在模具的主體和模具腔之間,模具含有內在表面涂層。在表面涂層中顆粒的尺寸通常小于50微米。在模具的主體中顆粒的尺寸可大于50微米。在一個實施方案中,在模具的主體中顆粒的尺寸大于1mm。在一個實施方案中,在表面涂層中顆粒的尺寸小于50微米,而在模具的主體中顆粒的尺寸多于50微米。通常,表面涂層為連續的內在表面涂層,使其更有效。比起模具的主體,內在表面涂層中鋁酸鈣的重量分數可多至少20%,氧化鋁的重量分數可少至少20%,并且鈣鋁石的重量分數可少至少50%。在內在表面涂層中單鋁酸鈣的重量分數可多于0.60,并且鈣鋁石的重量分數可小于0.10。在一個實例中,在內在表面涂層中單鋁酸鈣的重量分數為0.1-0.9;在內在表面涂層中二鋁酸鈣的重量分數為0.05-0.90;并且在內在表面涂層中鈣鋁石的重量分數為0.001-0.05。在內在表面涂層中單鋁酸鈣的提高的重量分數降低在鑄塑期間熔融合金與模具的反應速率。比起模具的主體,內在表面涂層中單鋁酸鈣的重量分數可多至少20%。比起模具的主體,內在表面涂層中氧化鋁的重量分數可少至少20%。在一個實例中,比起模具的主體,內在表面涂層中鋁酸鈣的重量分數可多至少20%,氧化鋁的重量分數可少至少20%,并且鈣鋁石的重量分數可少至少50%。在某些實施方案中,表面涂層的組成相以及模具的主體的組成相對于鑄件的性質是重要的。如本文公開的,在鑄塑期間,模具的表面涂層提供與合金最小的反應,結果是模具提供具有所需的組分性質的鑄件。鑄件的外部性質包括諸如形狀、幾何結構和表面光潔度等特征。鑄件的內部性質包括機械性質、微觀結構和低于臨界尺寸的缺陷(例如孔和內含物)。關于模具的表面涂層和模具的主體的組成相,出于至少兩個原因期望單鋁酸鈣(CaAl2O4)。首先,在模具制備的初始階段期間,單鋁酸鈣促進在水泥顆粒之間的液壓結合形成,并且該液壓結合在模具構造期間提供模具強度。第二,單鋁酸鈣經歷非常低速率的與基于鈦和鋁化鈦的合金的反應。在一個實施方案中,表面涂層包含單鋁酸鈣(CaAl2O4)、二鋁酸鈣(CaAl4O7)和鈣鋁石(Ca12Al14O33)和氧化鋁。在一個實施方案中,在表面涂層中顆粒的尺寸小于50微米。在表面涂層中,單鋁酸鈣(CaAl2O4)、二鋁酸鈣(CaAl4O7)的組合多于50重量%,并且氧化鋁濃度小于50重量%。在一個實施方案中,在表面涂層中存在多于30重量%單鋁酸鈣(CaAl2O4)。在表面涂層后面并且遠離模具腔的區域稱為模具的主體。在模具部分的該主體中,在一個實施方案中,單鋁酸鈣(CaAl2O4)、二鋁酸鈣(CaAl4O7)的組合小于50重量%,并且在模具的主體中氧化鋁濃度大于50重量%。用于鑄塑珠寶和牙齒假體的由熔融二氧化硅、方石英、石膏等組成的常規的熔模鑄造模具化合物不適于鑄塑反應性合金,例如鈦合金,因為在鈦和熔模鑄造模具之間存在反應。在熔融合金與模具之間的任何反應將劣化最終的鑄件的性質。劣化可簡單地為由于氣泡引起的差的表面光潔度,或者在更嚴重的情況下,可危害鑄件的化學性質、微觀結構和性質。挑戰在于生產不與鈦和鋁化鈦合金顯著反應的熔模鑄造模具。關于這一點,存在很少(若有的話)滿足結構鈦和鋁化鈦合金的需要的先前講述的陶瓷熔模鑄造化合物。需要不與鈦和鋁化鈦合金顯著反應的熔模鑄造模具。在先前方法中,為了降低常規的熔模鑄造模具化合物的限制,開發了若干另外的模具材料。例如,開發了氧化膨脹類型的熔模鑄造化合物,其中氧化鎂或氧化鋯用作主要組分,并且將金屬鋯加入到主要組成中以補償由于鑄塑金屬凝固引起的收縮。然而,現有技術熔模鑄造化合物具有限制。例如,出于若干原因,旨在通過金屬鋯的氧化膨脹補償由于鑄塑金屬凝固引起的收縮的熔模鑄造模具化合物難以實踐。首先,使用含有鋯的新熔模鑄造化合物在其表面上涂布蠟圖案,隨后將已涂布的蠟圖案嵌入常規的熔模鑄造化合物中,以試圖使鋯的所需量盡可能少;使用鋯涂布蠟非常困難并且不是高度可重復的。第二,復雜形狀部件的蠟不能以足夠均勻的方式涂布。此外,當熔模鑄造模具混合物圍繞涂布的層和圖案在外部放置時,涂布的層可脫離蠟,結果是鈦與外部放置的熔模鑄造模具混合物反應。比起使用外在表面涂層,使用內在表面涂層具有顯著的優點。用于鑄塑鈦合金的外在表面涂層通常為基于氧化釔的表面涂層或基于氧化鋯的表面涂層。具體地,用于鑄塑的模具中的外在表面涂層在模具加工(例如除去短效圖案和焙燒)和鑄塑期間可退化、裂紋和散裂。當模具填充熔融的金屬時,從外在表面涂層分離的表面涂層塊可變為被夾帶在鑄件中,并且陶瓷表面涂層變為在最終的零件中的包含物。包含物降低由鑄塑生產的部件的機械性能。鋁酸鈣水泥稱為水泥或粘合劑,在一個實施方案中,將其與氧化鋁顆粒混合,以制備可鑄塑的熔模鑄造模具混合物。在可鑄塑的熔模鑄造模具混合物中,鋁酸鈣水泥通常>30重量%;使用該比例的鋁酸鈣水泥為本公開的特性,因為其有利于形成內在表面涂層。申請人發現,選擇正確的鋁酸鈣水泥化學性質和氧化鋁配方在決定模具的性能方面是重要的。在一個實例中,就鋁酸鈣水泥而言,申請人發現,還需要具有特定量的氧化鈣(CaO),以使與鈦合金的反應最小化。在一個實施方案中,表面涂層包含粒度小于約50微米的鋁酸鈣水泥。在另一個實施方案中,鋁酸鈣水泥的粒度小于約10微米。在一個實施例中,模具的主體具有尺寸大于50微米的顆粒并且可含有氧化鋁。比起模具的主體,表面涂層具有較少的氧化鋁和較多的鋁酸鈣水泥。比起模具的主體,內在表面涂層中鋁酸鈣的重量分數可多至少20%,氧化鋁的重量分數可少至少20%,并且鈣鋁石的重量分數可少至少50%。在一個實例中,在內在表面涂層中單鋁酸鈣的重量分數為0.1-0.9;在內在表面涂層中二鋁酸鈣的重量分數為0.05-0.90;并且在內在表面涂層中鈣鋁石的重量分數為0.001-0.05。在內在表面涂層中提高的重量分數的單鋁酸鈣和二鋁酸鈣降低在鑄塑期間熔融合金與模具的反應速率。將初始水泥漿料混合至粘度為50-150厘泊。在一個實施方案中,粘度范圍為80-120厘泊。如果粘度太低,則漿料將不能保持所有的固體懸浮,并且將發生較重顆粒的沉降,并且在固化期間導致離析,并且不形成內在表面涂層。如果粘度太高,則鋁酸鈣顆粒可能不分配至短效圖案,并且不形成內在表面涂層。將含鋁酸鈣水泥和氧化鋁顆粒的最終漿料混合至粘度為約2000-8000厘泊。在一個實施方案中,該最終的漿料粘度范圍為3000-6000厘泊。如果最終的漿料/混合物粘度太高,則最終的漿料混合將不能圍繞短效圖案流動,并且模具的內腔將不適于鑄塑最終的所需零件。如果最終的漿料混合物粘度太低,則在固化期間將發生較重顆粒的沉降,并且在整個模具的主體中,模具將不具有所需的均勻組成。熔模鑄造模具由微型(<50微米)鋁酸鈣水泥顆粒、微型(<50微米)氧化鋁顆粒和較大規格(>100微米)氧化鋁顆粒的多相混合物組成。內在表面涂層不含任何大于50微米的氧化鋁顆粒。形成內在表面涂層,這是由于在模具制備期間,在基于水的熔模鑄造混合物中,在懸浮液中的微型水泥顆粒優先分配至短效/蠟圖案,并且形成富含微型顆粒(<50微米)的內在表面涂層,該微型顆粒(<50微米)包括單鋁酸鈣、二鋁酸鈣和氧化鋁顆粒。在一個實施方案中,在表面涂層中不存在大規格氧化鋁顆粒(>50微米)。漿料粘度和固體載荷為形成內在表面涂層的因素。在內在表面涂層中不存在大規格(>100微米)顆粒改進模具和所得到的鑄件的表面光潔度。在內在表面涂層中提高的重量分數的單鋁酸鈣和二鋁酸鈣降低在鑄塑期間熔融合金與模具的反應速率。在模具的主體中,鋁酸鈣水泥為粘合劑,認為粘合劑是在表面涂層后面的模具結構的主要骨架。其在模具中為連續的相,并且在固化和鑄塑期間提供強度。在一個實施方案中,模具組合物的主體包含微型(<50微米)鋁酸鈣水泥顆粒和較大規格(>100微米)氧化鋁顆粒。在另一個實施方案中,表面涂層組合物包含鋁酸鈣水泥。組成表面涂層的鋁酸鈣水泥包含至少三個相:單鋁酸鈣(CaAl2O4)、二鋁酸鈣(CaAl4O7)和鈣鋁石(Ca12Al14O33)。在一個實施方案中,表面涂層還可含有微型氧化鋁顆粒。在另一個實施方案中,在表面涂層后面的模具的主體包含單鋁酸鈣(CaAl2O4)、二鋁酸鈣(CaAl4O7)、鈣鋁石(Ca12Al14O33)和氧化鋁。氧化鋁可作為氧化鋁顆粒例如空心氧化鋁顆粒摻入。顆粒可具有一定范圍的幾何形狀,例如圓形顆粒或不規則的聚集體。氧化鋁粒度可小至10微米并且大至10mm。在一個實施方案中,氧化鋁由圓形顆粒和空心顆粒二者組成,因為這些幾何形狀提高熔模鑄造模具混合物的流動性。通常在模具的主體中氧化鋁粒度大于50微米。流動性影響在圍繞短效圖案傾倒和凝固熔模鑄造模具混合物期間水泥分配至短效圖案(例如蠟)的方式。流動性影響由模具生產的最終鑄件的表面光潔度和表面特征的保真度。如果初始水泥混合物的粘度太低,則漿料將不能保持所有的固體懸浮,將發生較重顆粒的沉降,并且導致在固化期間離析,并且不形成內在表面涂層。如果粘度太高,則鋁酸鈣顆粒不能分配至短效圖案,并且不形成內在表面涂層。如果最終的混合物粘度太高,則最終的漿料混合將不能圍繞短效圖案流動,在漿料混合物和圖案之間將截留空氣,模具的內腔將不適于鑄塑最終的所需零件。如果最終的漿料混合物粘度太低,則在固化期間將發生較重顆粒的沉降,并且在整個模具的主體中模具將不具有所需的均勻組成,并且危害所得到的鑄件的品質。產生表面涂層的鋁酸鈣水泥顆粒通常具有小于50微米粒度。粒度小于50微米具有若干優點,包括:首先,在模具混合和固化期間,細粒度促進形成液壓結合,第二,在焙燒期間,細粒度可促進顆粒間燒結,這可提高模具強度,第三,細粒度改進模具腔的表面光潔度。鋁酸鈣水泥粉末可以其內在形式或凝聚形式(例如噴霧干燥的附聚物)使用。在與較大規格氧化鋁混合之前,鋁酸鈣水泥還可與微型(<10微米)氧化鋁預先混合;在高溫焙燒期間,由于燒結,微型氧化鋁可提供強度提高。然而,如果氧化鋁顆粒分配至表面涂層,則可降低鑄件性質。例如,如果氧化鋁顆粒分配至表面涂層,使得比起模具的主體,內在表面涂層具有更多的氧化鋁,則熔融合金將以不期望的方式與氧化鋁反應,并且產生氣泡,氣泡產生表面缺陷和在鑄件本身內的缺陷。降低所得到的鑄件的性質,例如強度和疲勞強度。本發明公開的方法允許形成這樣的表面涂層,其在內在表面涂層中與在模具的主體中相比具有顯著較少的氧化鋁。從室溫到最終的焙燒溫度的對表面涂層和模具的處理還可為重要的,尤其是熱歷史和濕度分布圖。至焙燒溫度的加熱速率和在焙燒之后的冷卻速率是非常重要的。如果表面涂層和模具加熱得太快,則它們可在內部或外部或二者產生裂紋;在鑄塑之前表面涂層和模具裂紋是高度不期望的,其將至少產生差的表面光潔度。此外,如果模具和表面涂層加熱得太快,則模具的表面涂層可裂紋和散裂;這可在最壞的情況下導致在最終的鑄件中不期望的包含物,以及即使不存在包含物,也導致差的表面光潔度。如果在達到最大模具焙燒溫度之后,表面涂層和模具冷卻得太快,則表面涂層或模具的主體還可在內部或外部或二者產生裂紋。初始水泥混合物的固體載荷和最終的模具混合物的固體載荷對模具結構和在模具內形成內在表面涂層的能力具有重要的影響,如在以下段落中描述的。固體載荷的百分比定義為用百分比表示的除以在混合物中液體和固體的總質量的在混合物中的總固體。在一個實施方案中,在初始鋁酸鈣-液體水泥混合物中固體的重量百分比為約71%-78%。如果初始水泥漿料中的固體載荷小于約70%,則水泥顆粒將不保持懸浮,并且在模具的固化期間,水泥顆粒將與水分離并且在整個模具中,組合物將不均勻。與此相反,如果在水泥中固體載荷太高(例如大于約78%),則具有大規格氧化鋁的最終混合物的粘度將太高(例如大于約85%,取決于加入的大規格氧化鋁顆粒的量、尺寸和形態),并且混合物中的水泥顆粒將不能分配至模具內的短效圖案,并且將不形成內在表面涂層。在一個實施方案中,在具有大規格(在一個實施方案中,意指大于約50微米,在另一個實施方案中,意指大于約100微米)氧化鋁顆粒的最終鋁酸鈣-液體水泥混合物中固體的重量百分比為約75%-約90%。在一個實施方案中,在具有大規格氧化鋁顆粒的最終鋁酸鈣-液體水泥混合物中固體的重量百分比為約78%-約88%。在另一個實施方案中,在具有大規格氧化鋁顆粒的最終鋁酸鈣-液體水泥混合物中固體的重量百分比為約78%-約84%。在一個具體的實施方案中,在具有大規格氧化鋁顆粒的最終鋁酸鈣-液體水泥混合物中固體的重量百分比為約80%。模具和鑄塑方法通過配制陶瓷部件的熔模鑄造混合物,和將該混合物倒入含有短效圖案的容器中,來形成熔模鑄造模具。讓在圖案上形成的熔模鑄造模具徹底固化,以形成所謂的“生模具(greenmold)”。在圖案上形成內在表面涂層和熔模鑄造模具,并且讓它們徹底固化,以形成該生模具。通常,生模具的固化進行1小時-48小時的時間。隨后,通過熔融、溶解、點燃或其它已知的圖案去除技術,將短效圖案從生模具選擇性除去。用于蠟圖案去除的典型的方法包括烘箱脫蠟(小于150℃)、熔爐脫蠟(大于150℃)、蒸汽高壓釜脫蠟和微波脫蠟。對于鑄塑鈦合金和鋁化鈦及其合金,生模具隨后在超過600℃的溫度(例如600-1400℃)下焙燒超過1小時的時間段,優選2-10小時,以形成用于鑄塑的模具強度和除去模具中的任何不期望的殘余的雜質,例如金屬物類(Fe、Ni、Cr)和含碳物類。在一個實例中,焙燒溫度為至少950℃。焙燒模具的氣氛通常為環境空氣,但是可使用惰性氣體或還原氣體氣氛。焙燒過程還從模具中除去水并且將鈣鋁石轉化為鋁酸鈣。模具焙燒程序的另一個目的是在鑄塑前使保留在表面涂層和模具中的任何游離的二氧化硅最小化。其它目的是提高高溫強度和提高單鋁酸鈣和二鋁酸鈣的量。將模具從室溫加熱至最終的焙燒溫度,尤其是控制熱歷史。通常調節或控制至焙燒溫度的加熱速率和在焙燒后的冷卻速率。如果模具加熱得太快,則其可在內部或外部或二者產生裂紋;在鑄塑前的模具裂紋是高度不期望的。此外,如果模具加熱得太快,則模具的內表面可裂紋和散裂。這可導致在最終的鑄件中不期望的包含物,和即使不存在包含物,也導致差的表面光潔度。類似地,如果在達到最大溫度之后,模具冷卻得太快,則模具還可在內部或外部或二者產生裂紋。在本公開中描述的模具組合物特別適于鈦和鋁化鈦合金。在焙燒后和在鑄塑前,模具組合物的表面涂層和主體可影響模具性質,特別是對于組成相而言。在一個實施方案中,對于鑄塑目的,優選在模具中高重量分數的單鋁酸鈣,例如,0.15-0.8的重量分數。此外,對于鑄塑目的,期望使鈣鋁石的重量分數最小化,例如使用0.01-0.2的重量分數,因為鈣鋁石對水敏感,并且在鑄塑期間,其可提供水釋放和氣體產生的問題。在焙燒后,模具還可含有小重量分數的硅鋁酸鹽和硅鋁酸鈣。硅鋁酸鹽和硅鋁酸鈣的重量分數的總和在模具的主體中通常可保持小于5%,而在表面涂層中通常可保持小于0.5%,以使模具與鑄件之間的反應最小化。本公開的一方面為一種用于形成用于鑄塑含鈦制品的鑄塑模具的方法,所述方法包括:使鋁酸鈣與液體組合,以生產鋁酸鈣的漿料,其中在初始鋁酸鈣/液體混合物中固體的重量百分比為約70%-約80%,并且漿料的粘度為約50-約150厘泊;將氧化物顆粒加入到漿料中,使得在具有大規格(大于50微米)氧化物顆粒的最終的鋁酸鈣/液體混合物中固體的重量百分比為約75%-約90%;將漿料引入到含有短效圖案的模具腔中;和允許漿料在模具腔中固化,以形成含鈦制品的模具。在某些實施方案中,本公開的鑄塑模具組合物包含熔模鑄造模具組合物。熔模鑄造模具組合物包含近凈形狀含鈦金屬熔模鑄造模具組合物。在一個實施方案中,熔模鑄造模具組合物包含用于鑄塑近凈形狀鋁化鈦制品的熔模鑄造模具組合物。近凈形狀鋁化鈦制品包含例如近凈形狀鋁化鈦渦輪葉片。選擇正確的鋁酸鈣水泥化學性質和氧化鋁配方為在鑄塑期間模具的性能方面的因素。就鋁酸鈣水泥而言,可能需要使游離氧化鈣的量最小化,以使與鈦合金的反應最小化。如果在水泥中氧化鈣濃度小于約10重量%,則由于氧化鋁濃度太高,合金與模具反應,并且反應產生在鑄件中不期望的氧濃度水平、氣泡和在鑄塑部件中產生差的表面光潔度。在模具材料中較不期望游離的氧化鋁,因為游離的氧化鋁可與鈦和鋁化鈦合金積極地反應。如果在水泥中氧化鈣濃度大于50重量%,則模具可對從環境吸收水和二氧化碳敏感。因此,在熔模鑄造模具中氧化鈣濃度可通常保持低于50%。在一個實施方案中,在熔模鑄造模具的主體中氧化鈣濃度為10重量%-50重量%。在一個實施方案中,在熔模鑄造模具的主體中氧化鈣濃度為10重量%-40重量%。備選地,在熔模鑄造模具的主體中氧化鈣濃度可為25重量%-35重量%。在一個實施方案中,在表面涂層中CaO的組成為20-40重量%。在另一個實施方案中,在模具的表面涂層中氧化鈣濃度為15重量%-30重量%。二氧化碳可導致在加工期間和在鑄塑前在模具中形成碳酸鈣,并且在鑄塑操作期間,碳酸鈣不穩定。因此,模具中的水和二氧化碳可導致差的鑄塑品質。如果吸附的水水平太高,例如,大于0.05重量%,則當在鑄塑期間熔融的金屬進入模具時,釋放水并且其可與合金反應。這導致差的表面光潔度、鑄件中的氣泡、高氧濃度和差的機械性質。此外,一定量的水可引起模具未被完全填充。類似地,如果二氧化碳水平太高,則可在模具中形成碳酸鈣,并且當在鑄塑期間熔融的金屬進入模具時,碳酸鈣可分解,產生二氧化碳,其可與合金反應;如果釋放大量的二氧化碳,則氣體可引起模具未被完全填充。所得到的碳酸鈣在模具中小于1重量%。在鑄塑熔融的金屬或合金之前,通常將熔模鑄造模具預先加熱至模具鑄塑溫度,其取決于待鑄塑的具體部件幾何結構或合金。例如,典型的模具預熱溫度為600℃。通常,模具溫度范圍為450℃-1200℃;優選的溫度范圍為450℃-750℃,并且在某些情況下,該溫度為500℃-650℃。根據一方面,使用常規的技術,將熔融的金屬或合金倒入模具中,該技術可包括重力、反重力、壓力、離心技術和本領域技術人員已知的其它鑄塑技術。可使用真空或惰性氣體氣氛。對于復雜形狀的薄壁幾何形狀,優選使用高壓的技術。在通常將凝固的鋁化鈦或合金鑄件冷卻至小于650℃(例如,冷卻至室溫)時,將其從模具中移出并且使用常規的技術精加工,該技術例如噴砂處理和拋光。本公開的一方面為一種用于鈦和鈦合金的鑄塑方法,所述方法包括:得到包含鋁酸鈣和氧化鋁的熔模鑄造模具組合物,其中將鋁酸鈣與液體組合,以生產鋁酸鈣的漿料,并且其中在具有大規格氧化鋁的最終的鋁酸鈣/液體混合物中固體的重量百分比為約75%-約90%,并且其中所得到的模具具有內在表面涂層;將所述熔模鑄造模具組合物倒入含有短效圖案的容器中;固化所述熔模鑄造模具組合物;從模具中除去短效圖案;焙燒模具;將模具預熱至模具鑄塑溫度;將熔融的鈦或鈦合金倒入已加熱的模具中;使熔融的鈦或鈦合金凝固,并且形成凝固的鈦或鈦合金鑄件;和從模具中移出所述凝固的鈦或鈦合金鑄件。在一個實施方案中,要求保護通過本文教導的鑄塑方法制備的鈦或鈦合金制品。本公開的一方面涉及一種用于鈦和鈦合金的鑄塑方法,所述方法包括:得到包含鋁酸鈣和氧化鋁的熔模鑄造模具組合物;將所述熔模鑄造模具組合物倒入含有短效圖案的容器中;固化所述熔模鑄造模具組合物;從模具中除去短效圖案;焙燒模具;將模具預熱至模具鑄塑溫度;將熔融的鈦或鈦合金倒入已加熱的模具中;使熔融的鈦或鈦合金凝固;和從模具中移出凝固的鈦或鈦合金。在從模具中除去短效圖案和將模具預熱至模具鑄塑溫度之間,首先將模具加熱或焙燒至約600℃-約1400℃的溫度,例如約950℃或更高,隨后冷卻至室溫。在一個實施方案中,固化步驟在低于約30℃的溫度下進行1小時-48小時。除去短效圖案包括熔融、溶解、點燃、烘箱脫蠟、熔爐脫蠟、蒸汽高壓釜脫蠟或微波脫蠟的步驟。在一個實施方案中,在從模具中移出鈦或鈦合金之后,可使用噴砂處理或拋光來精加工模具。在一個實施方案中,在從模具中移出凝固的鑄件之后,通過X-射線或中子射線照相術檢查該鑄件。在鑄塑和精加工后,使凝固的鑄件經歷表面檢查和X-射線照相術,以檢測在鑄件內的任何位置處的任何表面下包含物顆粒。采用X-射線照相術來發現通過目視檢查鑄件的外表面不能檢測到的內含物。使用常規的X-射線設備使鋁化鈦鑄件經歷X-射線照相術(膠片或數字),以提供X-射線照片,隨后檢查或分析該照片,以確定在鋁化鈦鑄件中是否存在任何表面下內含物。備選地或除X-射線照相術以外,凝固的鑄件可經歷其它非破壞性測試,例如,常規的中子射線照相術。所描述的模具組合物提供少量的具有高中子吸收橫截面的材料。在一方面,制備鑄塑制品的中子射線照片。由于鈦合金鑄塑制品可基本上透過中子,模具材料通常將在所得到的中子射線照片中清楚地顯露。在一方面,認為中子暴露導致在射線照相上致密元素的“中子激活”。中子激活包括中子輻射與鑄件的射線照相上致密元素相互作用,以實現形成模具組合物的射線照相上致密元素的放射性同位素。然后可通過常規的放射性檢測裝置檢測放射性同位素,以計數在鑄塑制品中存在的任何射線照相上致密元素同位素。本公開的另一方面為一種用于形成用于鑄塑含鈦制品的鑄塑模具的方法。所述方法包括:使鋁酸鈣與液體(例如水)組合,以在液體中生產鋁酸鈣的漿料;將漿料引入含有短效圖案的容器中;和允許漿料在模具腔中固化,以形成含鈦制品的模具。在一個實施方案中,所述方法還包括,在將漿料引入模具腔之前,將氧化物顆粒(例如空心氧化物顆粒)引入到漿料中。所形成的模具可為生模具,并且所述方法還可包括焙燒生模具。在一個實施方案中,鑄塑模具包括熔模鑄造模具,例如,用于鑄塑含鈦制品。在一個實施方案中,含鈦制品包括鋁化鈦制品。在一個實施方案中,熔模鑄造模具組合物包括用于鑄塑近凈形狀鋁化鈦制品的熔模鑄造模具組合物。近凈形狀鋁化鈦制品可包括近凈形狀鋁化鈦渦輪葉片。在一個實施方案中,本公開涉及由本文教導的含鈦制品鑄塑模具組合物形成的模具。本公開的另一方面涉及一種在前述模具中形成的制品。本公開的又一方面為通過鑄塑方法制備的鈦或鈦合金鑄件,所述注塑方法包括:得到包含鋁酸鈣和氧化鋁的熔模鑄造模具組合物;將所述熔模鑄造模具組合物倒入含有短效圖案的容器中;固化所述熔模鑄造模具組合物;從模具中除去短效圖案;焙燒模具;將模具預熱至模具鑄塑溫度;將熔融的鈦或鈦合金倒入已加熱的模具中;使熔融的鈦或鈦合金凝固,以形成鑄件;和從模具中移出凝固的鈦或鈦合金鑄件。在一個實施方案中,本公開涉及一種通過在本申請中教導的鑄塑方法制備的鈦或鈦合金制品。表面粗糙度為代表鑄塑和機械加工的零件的表面完整性的重要指數之一。表面粗糙度通過以下表征:在通過光學輪廓術(opticalprofilometry)測量的指定區域中的中線平均粗糙度值“Ra”以及平均峰值與峰谷距離“Rz”。粗糙度值可在輪廓上或在表面上計算。輪廓粗糙度參數(Ra,Rq,...)更常見。使用用于描述表面的公式計算每一個粗糙度參數。在使用中存在許多不同的粗糙度參數,但是Ra到目前為止最常見。如本領域已知的,表面粗糙度與工具磨損相關。通常,表面精加工過程通過研磨和搪磨得到具有在0.1mm-1.6mm范圍的Ra的表面。最終的涂層的表面粗糙度Ra值取決于涂層或涂布制品的期望的功能。平均粗糙度Ra用高度的單位表示。在英制(英國)系統中,1Ra通常用英寸的“百萬分數”表示。這也稱為“微英寸”。本文所示的Ra值是指微英寸。Ra值為70對應于約2微米;而Ra值為35對應于約1微米。通常要求高性能制品(例如渦輪葉片、渦輪導葉(vane)/噴嘴、渦輪增壓器、往復發動機閥、活塞,等)的表面具有約20或更少的Ra。本公開的一方面為包含鈦或鈦合金并且跨越其表面區域的至少一部分具有小于20的平均粗糙度Ra的渦輪葉片。隨著將熔融的金屬越來越高地加熱,它們傾向于變得越來越具有反應性(例如,與模具表面進行不希望的反應)。這樣的反應導致形成污染金屬零件的雜質,這導致各種有害的后果。雜質的存在改變金屬的組成,使得其可能不能滿足期望的標準,從而不允許使用鑄塑塊用于預期的應用。此外,雜質的存在可有害地影響金屬材料的機械性質(例如,降低材料的強度)。此外,這樣的反應可導致產生表面紋飾,這導致在鑄塑塊的表面上大量不期望的粗糙度。例如,使用如本領域已知的用于表征表面粗糙度的表面粗糙度值Ra,在良好的工作條件下,利用不銹鋼合金和/或鈦合金的鑄塑塊通常呈現約100-200的Ra值。這些有害效應驅使人們使用較低的溫度來填充模具。然而,如果熔融的金屬的溫度加熱得不夠,則鑄塑材料可能冷卻得太快,導致不完全填充鑄塑模具。本公開的一方面涉及用于鑄塑含鈦制品的包含鋁酸鈣的模具組合物。模具組合物還包含空心氧化鋁顆粒。制品包括金屬制品。在一個實施方案中,制品包括含鋁化鈦的制品。在另一個實施方案中,制品包括鋁化鈦渦輪葉片。在又一個實施方案中,制品包括近凈形狀鋁化鈦渦輪葉片。在安裝之前,該近凈形狀鋁化鈦渦輪葉片可能需要很少或不需要材料去除。實施例通過參考以下實施例可以更容易地理解已一般性描述的本公開,包括這些實施例僅用于說明本公開的某些方面和實施方案的目的,而不旨在以任何方式限制本公開。圖1a和1b顯示在高溫焙燒后模具微觀結構的一個實施例。顯示在1000℃下焙燒的模具的橫截面的反向散射電子掃描電子顯微鏡圖像,其中圖1a表示存在的氧化鋁顆粒210、模具表面涂層212、模具的主體214和朝向模具腔的模具的內表面216。圖1b表示鋁酸鈣水泥220。微型鋁酸鈣水泥220提供模具的骨架結構。在一個實施例中,鋁酸鈣水泥包含單鋁酸鈣和二鋁酸鈣。圖2a和圖2b顯示在高溫焙燒后模具微觀結構的一個實施例。顯示在1000℃下焙燒的模具的橫截面的反向散射電子掃描電子顯微鏡圖像,其中圖2a表示作為表面涂層微觀結構的部分存在的鋁酸鈣水泥310。圖2b表示氧化鋁顆粒320并且顯示模具/模具腔的內表面322以及內在表面涂層區域324。圖3和4顯示在高溫焙燒后模具微觀結構的兩個實施例,顯示氧化鋁510(在圖3中)610(在圖4中)和單鋁酸鈣520(在圖3中)620(在圖4中),其中在一個實施例中,將模具焙燒,以使鈣鋁石含量最小化。熔模鑄造模具組合物和配方將鋁酸鈣水泥與氧化鋁混合,以產生熔模鑄造模具混合物,并且測試了熔模鑄造模具化學性質的范圍。在一個實施例中,熔模鑄造混合物由含70%氧化鋁和30%氧化鈣的鋁酸鈣水泥、氧化鋁顆粒、水和膠態二氧化硅組成。如圖5a所示,該方法包括使鋁酸鈣與液體組合,以在液體中生產鋁酸鈣的漿料705。在初始鋁酸鈣/液體混合物中固體的重量百分比為約70%-約80%,并且漿料的粘度為約50-約150厘泊。在一個實施方案中,將氧化物顆粒加入到漿料中707,使得在具有大規格(大于50微米)氧化物顆粒的最終鋁酸鈣/液體混合物中固體的重量百分比為約75%-約90%。將鋁酸鈣漿料引入到含有短效圖案的模具腔中710。讓漿料在模具腔中固化,以形成鈦或含鈦制品的模具715。在示于圖5b的另一個實施例中,該方法包括得到包含鋁酸鈣和氧化鋁的熔模鑄造模具組合物725。在一個實施例中,將鋁酸鈣與液體組合,以生產鋁酸鈣的漿料,其中在具有大規格氧化鋁的最終鋁酸鈣/液體混合物中固體的重量百分比為約75%-約90%。將熔模鑄造模具組合物倒入含有短效圖案的容器中730。將熔模鑄造模具固化,從而提供鑄塑模具組合物735。從模具中除去短效圖案740,并且將模具焙燒。將模具預先加熱至模具鑄塑溫度745,和將熔融的鈦或鈦合金倒入已加熱的模具中750。使熔融的鈦或鈦合金凝固,并且形成凝固的鈦或鈦合金鑄件755。最后,從模具中移出凝固的鈦或鈦合金鑄件760。在第一實施例中,用于制備熔模鑄造模具的典型的水泥漿料混合物由3000克[g]鋁酸鈣水泥(包含約10重量%的鈣鋁石、約70重量%的單鋁酸鈣和約20重量%的二鋁酸鈣)、1500g尺寸小于10微米的煅燒的氧化鋁顆粒、2450g直徑在0.5mm-1.0mm尺寸范圍的高純度氧化鋁顆粒、1650g去離子水和150g膠態二氧化硅組成。最終的模具混合物的固體載荷為80%,其中固體載荷定義為用百分比表示的針對在混合物中液體和固體的總質量標準化的在混合物中的總固體。具有所有組分但是不含大規格氧化鋁顆粒的初始水泥漿料混合物的固體載荷為72%。模具形成厚度為約100微米的內在表面涂層。該配方產生直徑約120mm并且長400mm的模具。設計模具配方,使得在焙燒時模具的表面涂層和模具的主體二者存在小于1%線性收縮。生產的模具具有小于2克/立方厘米的密度。典型的高純度煅燒的氧化鋁顆粒類型包括熔融的、板狀和磨細的氧化鋁。典型的合適的膠態二氧化硅包括RemetLP30、RemetSP30、Nalco1030、Ludox。生產的模具用于鑄塑具有良好表面光潔度的含鋁化鈦的制品,例如渦輪葉片。粗糙度(Ra)值小于100微英寸,并且氧含量小于百萬分之2000[2000ppm]。該配方產生了直徑約120mm并且長400mm的模具。該配方生產具有小于2克/立方厘米的密度的模具。模具具有由鋁酸鈣相組成的內在表面涂層,并且表面涂層厚度為約100微米。這樣生產的模具成功地用于鑄塑具有良好表面光潔度的鋁化鈦渦輪葉片;例如,其中Ra小于100,并且氧含量小于2000ppm。該配方生產具有小于2克/立方厘米的密度的模具。通過將鋁酸鈣水泥、水和膠態二氧化硅在容器中混合,制備了模具混合物。使用高剪切形式混合。如果未徹底混合,則水泥可膠化,并且降低流動性,使得模具混合物將不能均勻覆蓋短效圖案,并且將不產生內在表面涂層。當水泥在混合物中呈完全懸浮時,加入氧化鋁顆粒。當水泥在混合物中呈完全懸浮時,加入微型氧化鋁顆粒。當微型氧化鋁顆粒與水泥完全混合時,將較大尺寸(例如,0.5-1.0mm)氧化鋁顆粒加入,并與水泥-氧化鋁配方混合。最終混合物的粘度為形成高品質表面涂層的連續內在表面涂層的另一因素,因為其必須不能太低或太高。本公開的另一個關鍵的因素是水泥混合物的固體載荷和水的量。此外,在模具制備工藝步驟期間,可在所選的點使用加速劑和延遲劑。在混合后,以受控的方式將熔模鑄造混合物倒入含有短效蠟圖案的容器中。容器提供模具的外部幾何結構,并且短效圖案產生內部幾何結構。正確的倒入速度為進一步特征,如果速度太快,則空氣可被夾帶在模具中,如果速度太慢,則可發生水泥和氧化鋁顆粒分離。合適的倒入速度在約1-約20升/分鐘范圍。在一個實施方案中,倒入速度為約2-約6升/分鐘。在一個具體的實施方案中,倒入速度為約4升/分鐘。在第二實施例中,用于制備熔模鑄造模具的漿料混合物由3000g鋁酸鈣水泥(包含約10重量%的鈣鋁石、約70重量%的單鋁酸鈣和約20重量%的二鋁酸鈣)、1500g尺寸小于10微米的煅燒的氧化鋁顆粒、2650g直徑在0.5-1mm尺寸范圍的高純度氧化鋁空心顆粒、1650g去離子水和150g膠態二氧化硅組成。如第一實施例所述,混合后,以受控的方式將熔模鑄造混合物倒入含有短效蠟圖案的容器中。具有所有組分但是不含大規格氧化鋁顆粒的初始水泥漿料混合物的固體載荷為72%。最終的模具混合物的固體載荷為80.3%;這稍高于在實施例1中的相應的值。鋁酸鈣水泥的重量分數為42%,而氧化鋁的重量分數為58%。該配方產生了直徑約120mm并且長400mm的模具。隨后將具有內在表面涂層的模具固化和在高溫下焙燒。這樣生產的具有內在表面涂層的模具成功地用于鑄塑具有良好表面光潔度的鋁化鈦渦輪葉片;Ra小于100,并且氧含量小于2000ppm。該配方產生了具有小于1.8克/立方厘米的密度的模具。模具具有包含鋁酸鈣相的內在表面涂層。模具形成厚度為約100微米的內在表面涂層。設計模具配方,使得在焙燒時模具的表面涂層和模具的主體二者存在小于1%線性收縮。在混合物中摻入的重量輕的熔融氧化鋁空心顆粒提供低導熱性。氧化鋁空心顆粒提供具有降低的密度和較低的導熱性(導熱性示于在圖6中的附屬圖中)的模具。在模具中存在35重量%的空心氧化鋁顆粒。該配方生產了直徑約120mm并且長400mm的模具。隨后將模具固化并且在高溫下焙燒。生產的模具用于鑄塑具有良好的表面光潔度的含鋁化鈦的制品,例如渦輪葉片。粗糙度(Ra)值小于100,并且氧含量小于2000ppm。該配方生產了具有小于1.8克/立方厘米的密度的模具。作為從室溫到1000℃的溫度的函數,在圖6中將模具的主體的導熱性與氧化鋁的導熱性相比較。在所有溫度下,模具的主體的導熱性基本上小于氧化鋁的導熱性。使用熱線鉑電阻溫度計技術(ASTM測試C-1113)測量導熱性。在第三實施例中,用于制備熔模鑄造模具的漿料混合物由600g鋁酸鈣水泥(由約10重量%的鈣鋁石、約70重量%的單鋁酸鈣和約20重量%的二鋁酸鈣組成)、300g尺寸小于10微米的煅燒的氧化鋁顆粒、490g直徑在0.5-1mm尺寸范圍的高純度氧化鋁空心顆粒、305g去離子水和31gRemetLP30膠態二氧化硅組成。如第一實施例所述,混合后以受控的方式將熔模鑄造混合物倒入含有短效蠟圖案的容器中。該配方產生了直徑約120mm并且長150mm的用于較小部件的較小模具。隨后將模具固化并且在高溫下焙燒。這樣生產的模具成功地用于鑄塑具有良好表面光潔度的鋁化鈦渦輪葉片;Ra小于100,并且氧含量小于1600ppm。具有所有組分但是不合大規格氧化鋁顆粒的初始水泥漿料混合物的固體載荷為65%。該固體載荷低于制備可在模具中形成表面涂層的水泥漿料的理想限度。最終的模具混合物的固體載荷為77%;這稍低于用于生產模具的優選范圍。在第四實施例中,用于制備熔模鑄造模具的漿料混合物由2708g鋁酸鈣水泥(包含約10重量%的鈣鋁石、約70重量%的單鋁酸鈣和約20重量%的二鋁酸鈣)、1472g直徑在0.5-1mm尺寸范圍的高純度氧化鋁空心顆粒、1061g去離子水和96gRemet膠態二氧化硅LP30組成。如第一實施例所述,混合后,以受控的方式將熔模鑄造模具混合物倒入含有短效蠟圖案的容器中。具有所有組分但是不含大規格氧化鋁顆粒的初始水泥漿料混合物的固體載荷為70%。最終的模具混合物的固體載荷為79%;這稍低于在第一實施例中的相應的值。模具形成厚度為約100微米的內在表面涂層。該配方產生了用于較小部件的含有較小氧化鋁含量的較小模具。隨后將模具固化并且在高溫下焙燒。生產的模具用于鑄塑含鋁化鈦的制品,例如渦輪葉片。在第五實施例中,用于制備熔模鑄造模具的漿料混合物由1500g由Almatis公司生產的商業混合的80%鋁酸鈣水泥CA25C組成。CA25C產品標稱由70%鋁酸鈣水泥組成,所述70%鋁酸鈣水泥與氧化鋁混合以將組成調節至80%氧化鋁。使用460g去離子水和100g膠態二氧化硅生產初始固體載荷為73.5%的水泥漿料。當將漿料混合至可接受的粘度時,將550g尺寸范圍小于0.85mm并且大于0.5mm的氧化鋁空心顆粒加入到漿料中。使用由WashingtonMills公司生產的名稱為DuralumAB的產品。如第一實施例所述,混合后,以受控的方式將熔模鑄造模具混合物倒入含有短效蠟圖案的容器中。最終的模具混合物的固體載荷為79.1%;這在優選范圍的低端。將模具混合物倒入工具中,以生產具有4英寸直徑和6英寸長度的模具。模具形成內在表面涂層,但是模具的主體的組合物,特別是表面涂層的組合物含有太多二氧化硅。在模具中二氧化硅的主體組成為1.4重量%。在混合物中高濃度的膠態二氧化硅可導致在最終焙燒的模具中殘余的結晶二氧化硅和硅酸鹽(例如硅鋁酸鈣和硅鋁酸鹽)。模具、特別是表面涂層的高二氧化硅含量提供該模具配方的兩個限制。首先,在焙燒時可發生收縮,并且這導致產生多個問題,例如在表面涂層中的裂紋和部件的尺寸控制。第二,當在鑄塑期間填充模具時,在表面涂層中的高二氧化硅含量可引起與熔融的鈦和鋁化鈦合金反應;該反應導致不可接受的鑄件品質。在第六實施例中,使用由1500g鋁酸鈣水泥CA25C、510g水和50gRemetLP30膠態二氧化硅組成的漿料混合物,生產了直徑4英寸并且長度6英寸的模具。比起在前面的實施例中的配方,該混合配方具有較低的膠態二氧化硅濃度。在模具中二氧化硅的主體組成為0.7重量%。使用商業混合的80%鋁酸鈣水泥CA25C。生產了初始固體載荷為73.0%的水泥漿料。在這一點上,將550g尺寸范圍小于0.85mm并且大于0.5mm的DuralumAB氧化鋁空心顆粒加入到漿料中。最終的模具混合物的固體載荷為80.2%。如第一實施例所述,混合后,以受控的方式將熔模鑄造模具混合物倒入含有短效蠟圖案的容器中。在模具中二氧化硅的主體組成為0.7重量%。模具形成內在表面涂層,該內在表面涂層與在前面的實施例中的相比具有較低的二氧化硅含量。模具、特別是內在表面涂層的較低的二氧化硅含量提供對鑄塑鈦和鋁化鈦合金優選的模具。在第七實施例中,使用由4512g鋁酸鈣水泥CA25C、1534g水和151gLP30膠態二氧化硅組成的漿料混合物,生產了直徑100毫米并且長度400毫米的模具。生產了初始固體載荷為73.0%的水泥漿料。使用商業混合的80%鋁酸鈣水泥CA25C。在這一點上,將2452g尺寸范圍小于0.85mm并且大于0.5mm的DuralumAB氧化鋁空心顆粒加入到漿料中。如第一實施例所述,混合后,以受控的方式將熔模鑄造模具混合物倒入含有短效蠟圖案的容器中。最終的模具混合物的固體載荷為81%。在模具的主體和模具的表面涂層二者中,沿著模具的16英寸長度,模具具有均勻組成。在模具中二氧化硅的主體組成為0.6重量%。模具形成具有低二氧化硅含量的內在表面涂層。模具、特別是內在表面涂層的低二氧化硅含量提供對鑄塑鈦和鋁化鈦合金優選的模具。在模具中氧化鋁空心顆粒的重量百分比為35%。模具形成厚度為約100微米的內在表面涂層。在焙燒時模具經歷小于1%線性收縮。在第八實施例中,使用由765g市售可得的鋁酸鈣水泥Rescor780和RemetLP30膠態二氧化硅組成的漿料混合物,生產了直徑100毫米并且長度150毫米的模具。Rescor780由Cotronics,Inc生產。初始水泥漿料與LP30混合,并且具有76%的初始固體載荷。當初始漿料已混合至合適的粘度時,加入1122gZiralcast95。最終的模具混合物的固體載荷為81%。如第一實施例所述,混合后,以受控的方式將熔模鑄造混合物倒入含有短效蠟圖案的容器中。氧化鋁可鑄耐火材料Ziralcast-95由ZircarCemarics,Inc生產。Ziralcast-95為與熔融氧化鋁空心顆粒混合的高純度氧化鋁水泥。ZIRALCAST-95含有約44重量%氧化鋁空心顆粒和56重量%氧化鋁水泥;氧化鋁空心顆粒尺寸大于在前面的實施例中使用的尺寸,通常大于1mm。這樣生產的該模具配方具有一些吸引人的特性,但是其具有若干限制。首先,模具中的內在表面涂層比期望的薄;這是由于在傾倒之前最終的混合物的固體載荷高。第二,在模具混合物中存在太多的膠態二氧化硅,并且這導致在焙燒后在模具的主體中和在最終的模具的表面涂層中太多二氧化硅和所得到的硅酸鹽,例如硅鋁酸鈣。模具、特別是表面涂層的高二氧化硅和硅酸鹽含量提供該模具配方的兩個限制。首先,在焙燒時可發生收縮,并且這導致多個問題,例如在表面涂層中的裂紋和部件的尺寸控制。第二,當在鑄塑期間填充模具時,在表面涂層中的高二氧化硅含量可引起與熔融的鋁化鈦合金反應;該反應導致不可接受的鑄件品質。最后,氧化鋁空心顆粒尺寸太大,并且這降低所得到的混合物的流動性。較低的流動性導致較薄的內在表面涂層,并且所得到的模具產生具有較低品質的鑄件。在第九實施例中,使用2708g鋁酸鈣水泥Secar80、820g去離子水和80gLP30膠態二氧化硅生產了漿料混合物。Secar80水泥為市售可得的水硬水泥,其中氧化鋁含量為約80%。Secar80由Kerneos公司生產,它們以前稱為LaFarge。通過固態反應制備鋁酸鈣水泥熟料。燒結的熟料隨后與高表面積氧化鋁混合,以產生能夠促成高溫強度的水硬水泥。Secar80的主要礦物學相為鋁酸鈣(CaAl2O4)、二鋁酸鈣(CaAl4O7)和氧化鋁(Al2O3)。在第十實施例中,使用由4500g鋁酸鈣水泥CA25C和1469g去離子水組成的漿料混合物,生產了直徑約100毫米并且長度約400毫米的模具。生產了初始固體載荷為75.3%的水泥漿料。使用商業混合的80%鋁酸鈣水泥CA25C。在這一點上,將2445g尺寸范圍小于0.85mm并且大于0.5mm的DuralumAB氧化鋁空心顆粒加入到漿料中。如第一實施例所述,混合后,以受控的方式將熔模鑄造模具混合物倒入含有短效蠟圖案的容器中。最終的模具混合物的固體載荷為81%。在模具的主體和模具的表面涂層二者中,模具沿著模具的16英寸長度具有均勻組成。在模具中氧化鋁空心顆粒的重量百分比為35%。在焙燒時模具經歷小于1%線性收縮。該模具適于鑄塑。使用2708gSecar80,生產1初始固體載荷為73.0%的水泥漿料。使用該水泥不可能產生可生產具有優選的內在表面涂層的模具的漿料。如果熔模鑄造模具混合物的工作時間太短,則不存在足夠的時間來制備復雜形狀部件的大模具。如果熔模鑄造模具混合物的工作時間太長并且鋁酸鈣水泥不足夠快地固化,則可發生微型水泥和大規格氧化鋁的分離,這可導致其中配方變化并且所得到的模具性質不均勻的離析模具。膠態二氧化硅可影響鋁酸鈣相與水的反應速率,并且在固化期間,其還可影響模具強度。在模具制備期間,鋁酸鈣相與水的該反應速率控制熔模鑄造模具混合物的工作時間。該時間為約30秒-約10分鐘。如果熔模鑄造模具混合物的工作時間太短,則不存在足夠的時間來制備復雜形狀部件的大模具,并且不形成連續的內在表面涂層。如果熔模鑄造模具混合物的工作時間太長并且鋁酸鈣水泥不足夠快地固化,則可發生微型水泥和大規格氧化鋁的分離,這可導致其中配方變化并且所得到的模具性質不均勻的離析模具;其還可導致具有不連續或在組成和性質上變化的表面涂層的不期望的狀態。組成模具的連續表面涂層并且提供用于模具主體的粘合劑的水泥中的組成相為本公開的特性。在鋁酸鈣水泥中的三個相包括單鋁酸鈣(CaAl2O4)、二鋁酸鈣(CaAl4O7)和鈣鋁石(Ca12Al14O33),本發明人進行該選擇以實現若干目的。首先,該相必須溶解或部分溶解,并且形成在隨后的熔模鑄造模具制備漿料中可支撐所有聚集體相的懸浮液。第二,在傾倒后,該相必須促進模具的凝固或固化。第三,在鑄塑期間和在鑄塑之后,該相必須為模具提供強度。第四,該相必須呈現與在模具中鑄塑的鈦合金最小的反應。第五,模具必須具有與鈦合金鑄件匹配的合適的熱膨脹,以使在凝固后冷卻期間產生的零件上的熱應力最小化。在模具中和在模具的表面涂層中的鋁酸鈣水泥/粘合劑中的三個相為單鋁酸鈣(CaAl2O4)、二鋁酸鈣(CaAl4O7)和鈣鋁石(Ca12Al14O33)。將鈣鋁石摻入到模具中,因為其為快凝固鋁酸鈣,并且在固化的早期階段期間為表面涂層和模具的主體提供強度。固化必須在低溫下進行,因為短效蠟圖案對溫度敏感,并且在超過約35℃的熱暴露時失去其形狀和性質。優選在低于30℃的溫度下固化模具。應理解的是,以上描述旨在為說明性的而不是限制性的。例如,上述實施方案(和/或其多方面)可彼此組合使用。此外,在不背離其范圍的情況下,可進行許多修改以使具體的情況或材料適于各種實施方案的教導。雖然本文描述的材料的尺寸和類型旨在限定各種實施方案的參數,它們絕不是限制性的而僅為示例性的。在回顧以上描述后,許多其它實施方案對于本領域技術人員來說是顯而易見的。因此,應參考所附權利要求以及這些權利要求所享有的等價物的全部范圍來確定各種實施方案的范圍。在所附權利要求中,術語“包括”和“其中”用作各自的術語“包含”和“其中”的易懂的英語等價物。此外,在所附權利要求中,術語“第一”、“第二”和“第三”等僅用作標記,并且不旨在對它們的對象強加數字要求。此外,所附權利要求的限制不以手段加功能格式書寫,并且不旨在基于35U.S.C.§112,第六段來解釋,除非并且直到這類權利要求限制明確使用短語“用于...的手段”,其中間接著陳述缺乏其它結構的功能。應理解的是,根據任何具體的實施方案,不必實現所有的上述這類目標或優點。因此,例如,本領域技術人員將認識到,可以實現或優化本文教導的一個優點或一組優點的方式,體現或進行本文描述的系統和技術,而不必實現本文可能教導或提出的其它目標或優點。雖然已結合僅有限數量的實施方案詳細描述了本發明,應容易理解的是,本發明不局限于這些公開的實施方案。相反,可修改本發明以結合前面未描述但與本發明精神和范圍匹配的許多變化、改變、替代或等價排列。此外,雖然已描述了本發明的各種實施方案,應理解的是,本公開的多方面可僅包括一些所描述的實施方案。因此,本發明不應看作是受前述描述限制,而是僅受所附權利要求的范圍限制。該書面描述使用實施例來公開本發明(包括最佳方式),并且還使本領域任何技術人員能夠實踐本發明,包括制備和使用任何裝置或系統和進行任何結合的方法。本發明的可取得專利的范圍由權利要求限定,并且可包括本領域技術人員想到的其它實施例。如果它們具有與權利要求的字面語言沒有不同的結構要素,或者如果它們包括與權利要求的字面語言具有非實質差異的等價結構要素,這些其它實施例旨在在權利要求的范圍內。