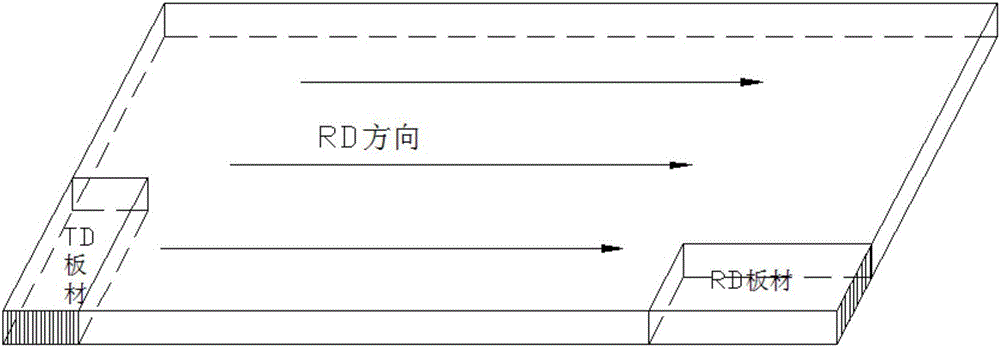
本發明屬于鋅合金板加工領域,具體涉及高強韌低膨脹鋅基耐磨合金薄板的加工方法;特別涉及ZA33鋅基耐磨合金薄板軋制方法。
技術領域:
鋅基耐磨合金主要是針對替代市場中大量應用的錫青銅產品,為了進一步提高性能,降低成本,升級產品。鋅基耐磨合金、不僅強度,塑性優于錫青銅,而且摩擦系數小,在磨擦產生的熱效應相對也較小,膨脹系數低,尺寸穩定性好。其薄板更可替代機械裝配制造行業聚四氟耐磨材質的軌道板,提高軌道板的穩定性和使用壽命。現如今鋅基耐磨合金薄板生產主要以機械加工為主,一方面加工尺寸會受到限制,即機械加工方法制造薄板難度大。另一方面加工成本也相應極具增加,嚴重限制了耐磨合金薄板的批量生產。鋅合金薄板的生產主要采用機械加工的方法,既費時又費力。現如今鋅基耐磨合金薄板軋制還未取得成功,耐磨合金3mm以下薄板軋制過程中,一般會出現微裂紋或邊界開裂,使得板材軋制過程進行不下去,同時也會減弱其耐磨性能。以現有鋅基合金軋制工藝對其進行軋制,單道次變形量達到30%時,會出現裂紋,隨著軋制量加大裂紋會逐漸擴大,以至于板材成形困難。技術實現要素:本發明要解決因鋅合金不易塑性變形,現有的軋制技術對于軋下變形量達到或超過30%時,板材就會開裂,難于進一步加工的問題;而提供一種高強韌低膨脹鋅基耐磨合金薄板的軋制方法。本發明的高強韌低膨脹鋅基耐磨合金薄板的軋制方法是由下述步驟完成的:步驟一、對鑄態坯料進行均勻化退火,冷卻至室溫,然后連續熱軋至板厚為4±0.2mm,得到軋制薄板用預制板材;步驟二、對步驟一獲得的預制板材進行多道次熱軋到3mm以下,其中,每道次軋制結束后直接預熱,預熱后進行下一道次軋制;其中步驟二的熱軋溫度比步驟一的熱軋溫度低50~60℃。步驟一中在360℃條件下對鑄態坯料均勻化退火12~15小時。連續熱軋的初軋溫度為320℃。步驟一中連續熱軋的單道次變形量為25%~30%。步驟二中每道次熱軋的預熱溫度為210℃~250℃。步驟二中每道次的變形量為30%~40%。本發明采用分級軋制的方法,即通過一次加熱,連續軋制的方法把板材軋制到4mm左右,然后采用每道次加熱的方法解決薄板軋制開裂的難題,板厚軋制最終尺寸為0.5mm-3mm,為耐磨鋅合金薄板的生產節約了時間,同時降低了耐磨鋅合金薄板的生產成本。由于軋制過程可以連續進行,與機械加工相比,提高了生產效率,并可以大批量連續生產,而且軋制尺寸不會受到限制。附圖說明圖1是拉伸試樣尺寸圖;圖2磨損試樣的截取位置及方向圖;圖3退火前鑄態坯料的拉伸斷口形貌;圖4軋制后薄板的斷口形貌(RD方向)。具體實施方式具體實施方式一:本實施方式對ZA33鋅基耐磨合金薄板軋制;具體的軋制方法是由下述步驟完成的:步驟一、在360℃條件下對厚度為24mm的鑄態坯料進行均勻化退火12h,冷卻至室溫,將鑄態坯料加熱到320℃后以30%道次變形量,經5個道次連續熱軋至板厚為4mm,每次變形之前不用重復加熱,得到軋制薄板用預制板材。步驟一的軋制方案如表1所示:表1厚板熱軋方案道次(變形量30%)1st2nd3th4th5th板厚/mm16.811.88.25.84在軋制前對板材進行360℃均勻化退火12個小時。退火后的鋅基耐磨合金初軋溫度為320℃,可以有效控制軋制過程中板材不出現開裂的情況,同時其橫向和縱向耐磨性能并沒有太大變化。步驟二、對步驟一獲得的預制板材進行多道次熱軋軋制到0.5mm厚,每道次采用道次變形量為40%,每道次軋制結束后直接預熱至230℃,預熱后進行下一道次軋制。軋制方案如表2所示。表2薄板多道次溫軋方案道次(變形量40%)1st2nd3th4th板厚/mm2.41.50.90.5板材軋制前后的力學性能和磨損量對比表3可以看出,除延伸率變化較大,其余力學性能都變化不大,而磨損量變化也不大,而且還有小幅提升,可見,該工藝在板材軋制后并沒有損失耐磨性。表3軋制前后板材的力學性能和磨損量對比為了使得軋制過程中變形量加大,在厚板軋制狀態可以一次性預熱板材,預熱溫度為320℃,單道次變形量可以在30%,并且每道次軋制不用重新預熱板材。但是板材在4mm以下軋制時,每道次軋制都需要預熱,預熱溫度為230℃,每道次的變形量可以達到40%,板材可以終軋到1mm以下。采用下述試驗驗證發明效果試驗所用初始材料為Zn-Al-Cu系高鋁鋅合金鑄造坯料,其成分如表4所示。鑄坯尺寸為24mm×80mm×150mm,軋制前進行360℃×12h均勻化退火。表4鋅鋁合金的化學成分(wt%)元素AlCuFeZn含量33.134.510.18Bal.軋制試驗在雙輥軋機上進行,軋輥尺寸為Ф220×360mm,軋制時軋輥線速度為5m/min。試驗過程中,通過軋機上裝配的壓力傳感器記錄軋制力的變化,通過紅外線感應溫度測量裝置測量軋制溫度。板材軋制工藝采用分級軋制,即厚板軋制工藝和薄板軋制工藝。厚板軋制工藝如表1所示,將24mm厚的鑄態坯料經過多道次,每道次變形量為30%最終軋制到4mm厚。軋制前對鑄態坯料進行360℃×12h均勻化退火,始軋溫度為320℃。即第1道次軋制前將板材加熱到320℃,隨后各道次間板材進行自然冷卻,保證每次軋制低于前一道次的軋制溫度。薄板軋制工藝如表2所示,板材經多道次軋制將板材軋制到0.5mm厚。初始板材厚度為4mm,采用道次變形量為40%,軋制過程中,軋制溫度一直保持為230℃,每道次軋制前將板材自然冷卻到室溫。常溫拉伸試驗在Instron5569電子萬能材料試驗機上進行,分別選取板材的軋向和橫向進行測試,拉伸速度1.5mm/min,并使用引伸計對變形量進行精確測量。按照國家標準,每種條件采用3組試樣重復拉伸,最后取其平均值。圖1所示為拉伸試樣的尺寸與取樣部位。板材的摩擦磨損試驗在УТИTB-100型銷-盤式摩擦磨損試驗機上進行,試樣尺寸有兩種,鑄態坯料為Ф5×20mm,軋后板材為0.5×5×20mm,分別截取RD與TD兩個方向,試驗前使用800#金相砂紙將待磨表面磨平。對磨材料使用GCr15圓盤(硬度HR62~65),試驗載荷40N,速度0.8m/s,摩擦行程1km,試驗過程中不添加任何潤滑劑。摩擦過程中的摩擦力通過傳感器進行實時測量,并使用SartiusMicr電子天平(精度為10~5g)稱量磨損前后的試樣質量,用以計算累計磨損量。圖2給出了試樣的截取位置與方向。退火前鑄態坯料的拉伸斷口形貌如圖3所示;軋制后薄板的斷口形貌(RD方向)如圖4所示。由圖3可知,鑄態坯料的斷裂主要以撕裂棱為主,存在許多解理小平面,為介于韌窩與解理之間的準解理斷裂。斷口表面隨機分布著微孔及大塊第二相,第二相為解理斷裂。由圖4可以看到斷口表面凹凸不平,幾乎整個斷口表面都布滿韌窩,這是塑性較好的表現,有明顯的沿軋制方向分布的特征。基體上布滿了小而淺的韌窩,在密集的淺且小的韌窩之間,分布著深不見底的空洞。此空洞為大韌窩,板材表面布滿韌窩是塑性較好的一個重要表現,與此同時,零散分布深而大的韌窩則進一步體現了軋后板材良好的塑性。與板材拉伸后抗拉強度提高正好對應。當前第1頁1 2 3