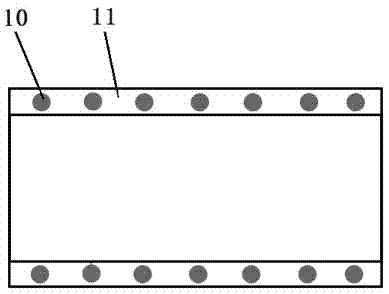
一種高壓旋轉壓縮-擴展擠壓大塑性變形成形裝置技術領域本發明一種高壓旋轉壓縮-擴展擠壓大塑性變形成形裝置,屬于金屬大塑性變形加工裝置技術領域。
背景技術:隨著航空航天、軍事和交通工具的快速發展,對材料的性能提出了更高的要求,因此制備高性能金屬材料是當今研究的熱點。目前提高材料力學性能的主要途徑有合金化、熱處理、形變強化和細晶強化等方法。研究表明單純依賴某一兩種強化機制來提高材料的綜合性能是有限的,將多種強化機制有機組合,不僅能充分挖掘材料的潛在性能,也是材料科學發展的必然趨勢。大塑性變形方法具有較強的晶粒細化能力,通過強烈的剪切變形,使多晶金屬材料內部組織細化至亞微米級(100nm-1.0μm)甚至納米級(<100nm),與傳統材料相比,超細晶材料具有優良的力學性能。同時大塑性變形使材料內部大角度晶界所占比例增大,從多方面改善了材料的性能。因此,大塑性變形對合金強化是多種強化機制共同作用的結果,強化效果顯著。目前大塑性變形方法主要有:等通道轉角擠壓(ECAP)、累積疊軋焊和多向鍛造等。ECAP在大塑性變形方法中最受關注且發展最快,其原理是將試樣在一定擠壓力作用下通過兩個軸線相交且截面尺寸相等并成一定角度的通道,使試樣發生純剪切變形,進而達到細化晶粒的目的。目前,越來越多的新型ECAP得到發展,如反復側邊擠壓、連續剪切及等徑角軋制等。雖然ECAP方法引起了廣泛關注,但是目前仍存在著許多問題:(1)ECAP生產效率不高。研究結果表明,為了使材料晶粒細化,提高材料性能,一般要經過多道次ECAP擠壓。但ECAP過程本身是不連續的,因此,中間過程復雜,生產效率低;(2)ECAP模具成本較高。ECAP擠壓過程中模具的磨損比較大,加工成本較高;(3)制備材料尺寸受限。由于受擠壓模具及擠壓桿尺寸的限制,難以制備大尺寸制品;(4)試驗原材料浪費比較嚴重。試樣擠壓后會沿擠壓方向伸長,當伸長的試樣再經ECAP時,容易發生開裂、脫落,導致材料浪費;(5)試樣表面質量會受影響。實驗一般采用MoS2作為潤滑劑,試樣在擠壓后表面會擠入黑色MoS2顆粒,表面清潔程度會受到影響。因此開發短流程、能夠制備大尺寸及多種截面制品的新型大塑性成形裝置,具有重要意義。
技術實現要素:本發明克服現有技術的不足,所要解決的技術問題是提供一種能夠實現連續生產的大塑性變形成形裝置。為解決上述技術問題,本發明所采用的技術方案為:一種高壓旋轉壓縮-擴展擠壓大塑性變形成形裝置,包括旋轉擠壓機、壓縮-擴展擠壓筒和擠壓模具;所述壓縮-擴展擠壓筒外部設置有加熱裝置,所述加熱裝置用于給壓縮-擴展擠壓筒加熱;所述壓縮-擴展擠壓筒通過機架固定在底座上;所述壓縮-擴展擠壓筒內部設置有壓縮-擴展腔、進料段和擠壓模具,所述壓縮-擴展腔由壓縮段和擴展段組成,壓縮段位于壓縮-擴展擠壓筒的進料段與擴展段之間,且壓縮段的直徑比所述進料段的直徑和擴展段的直徑都小;壓縮段與進料段和擴展段分別通過一段錐形過渡腔連接;擠壓模具設置在壓縮-擴展擠壓筒內部且位于擴展段的末端;所述旋轉擠壓機也固定在底座上,旋轉擠壓機的擠壓桿的直徑與所述進料段的直徑吻合,所述擠壓桿能夠伸入進料段中。工作過程如下:啟動加熱裝置,對壓縮-擴展擠壓筒進行預熱,同時將原料投放在進料段中進行保溫預熱,此時擠壓桿伸入進料段處就位,然后開動旋轉擠壓機,將擠壓桿在高速旋轉下向前推動,原料在旋轉和擠壓的雙重作用下,逐漸被壓入壓縮段,壓縮段的物料隨之進入擴展段得到擴展,擴展之后的原料在擠壓作用下通過擠壓模具成型。原料在最終進入模具的塑形部分之前,一直在擠壓桿的高速旋轉作用下進行旋動扭曲,并且經過壓縮-擴展腔的壓縮-擴展過程,實現原料的大塑性變形,高壓旋轉和壓縮-擴展擠壓相結合,實現了高效制備超細晶高性能合金制品。同時,本發明的成形過程不需要間斷,對于某種材料、尺寸的合金產品,根據性能的要求,只需要通過適當的模擬和試驗,就能確定合適的壓縮-擴展比和旋轉轉速,通過本發明的裝置可以實現一次成形制得產品。制備過程簡單,生產效率顯著提高。另外不需要添加潤滑劑等,產品表觀質量優秀。相應的,本發明的大塑性變形成形裝置還應當包括對擠出的型材進行定型和冷卻的冷卻系統,以及對整個裝置的工作過程和工藝參數進行設定和調整的控制系統。冷卻系統的類型以及控制系統是可以根據實際生產需要進行設計和選擇的。加熱裝置的目的是給壓縮-擴展擠壓筒加熱,最簡單的結構包括電阻絲和耐火磚,耐火磚貼覆在壓縮-擴展擠壓筒的外壁上形成耐火磚覆層,電阻絲螺旋盤繞在耐火磚覆層內。但是基于加熱裝置的設置目的,也可以選擇其他類型的加熱方式和配套裝置。為了不對加熱裝置構成影響,機架可以選擇常規的結構,包括前固定板、后固定板和固定橫梁,前固定板和后固定板的四角通過四根固定橫梁連接,將壓縮-擴展擠壓筒固定在前固定板和后固定板之間。本發明的核心結構是壓縮-擴展擠壓筒,最主要的就是壓縮段和擴展段。基于常規的型材尺寸,壓縮段的直徑可以在10-390mm范圍內選擇,相應的,擴展段的直徑則在20-400mm范圍內選擇;進料段的直徑也可以在20-400mm范圍內選擇,同時,需要伸入進料段中的擠壓桿的直徑優選比進料段的直徑小0.2mm。擠壓模具的入口直徑應當與擴展段的直徑一致。擠壓桿、擠壓筒和擠壓模具的材料、性能要求等,可以根據通常處理的原料的性質進行選擇和設計。例如:擠壓桿材質可選H13、3Cr2W8V、3Cr3Mo3W2V、Cr4W5Mo2V。壓縮-擴展擠壓筒材質可選H13、3Cr2W8V、3Cr3Mo3W2V、Cr4W5Mo2V模具鋼。擠壓模具材質可選H13、3Cr2W8V、3Cr3Mo3W2V、Cr4W5Mo2V。與現有技術相比本發明具有以下有益效果。1、將高壓旋轉和壓縮-擴展擠壓相結合,實現了高效制備超細晶高性能合金制品。2、對成形過程溫度進行控制,實現了成形過程的穩定性,同時也實現了對制品內部組織的控制。3、成本低,工藝流程短,更容易實現工業化生產。4、可以連續制備大尺寸超細晶金屬制品。附圖說明下面結合附圖對本發明作進一步說明。圖1是高壓旋轉壓縮-擴展擠壓大塑性變形成形裝置示意圖。圖2是加熱裝置示意圖。圖3是制備的Al-0.5Sc合金管材及其內部組織:(a)擠壓筒溫度300℃,擠壓速度為5mm/min,冷卻水流量為15L/min,制備的超細晶合金管材;(b)該管材對應的內部組織。圖中:1為旋轉擠壓機,2為擠壓桿,3為機架,4為加熱裝置,5為壓縮-擴展擠壓筒,6為擠壓模具,7為冷卻系統,8為控制器,9為底座,10為電阻絲,11為耐火磚。具體實施方式以下結合具體實施例對本發明作進一步說明。實施例1如圖1和圖2所示,一種高壓旋轉壓縮-擴展擠壓大塑性變形成形裝置,包括旋轉擠壓機1、壓縮-擴展擠壓筒5和擠壓模具6;所述壓縮-擴展擠壓筒5外部設置有加熱裝置4,所述加熱裝置4用于給壓縮-擴展擠壓筒5加熱;所述壓縮-擴展擠壓筒5通過機架3固定在底座9上;所述壓縮-擴展擠壓筒5內部設置有壓縮-擴展腔,所述壓縮-擴展腔由壓縮段和擴展段組成,壓縮段位于壓縮-擴展擠壓筒5的進料段與擴展段之間,且壓縮段的直徑比所述進料段的直徑和擴展段的直徑都小;壓縮段與進料段和擴展段分別通過一段錐形過渡腔連接;擠壓模具6設置在壓縮-擴展擠壓筒5內部且位于擴展段的末端;所述旋轉擠壓機1也固定在底座9上,旋轉擠壓機1的擠壓桿2的直徑與所述進料段的直徑吻合,所述擠壓桿2能夠伸入進料段中;還包括冷卻系統7和控制系統8;所述冷卻系統7用于對經過擠壓模具6擠出的型材進行定型和冷卻;所述控制系統8用于控制大塑性變形成形裝置動作以及參數的設定和調控;所述加熱裝置4包括電阻絲10和耐火磚11,耐火磚11貼覆在壓縮-擴展擠壓筒5的外壁上形成耐火磚覆層,電阻絲10螺旋盤繞在耐火磚覆層內;所述機架3包括前固定板、后固定板和固定橫梁,前固定板和后固定板的四角通過四根固定橫梁連接,所述壓縮-擴展擠壓筒5固定在前固定板和后固定板之間。實施例2采用本發明裝置制備Al-0.5Sc合金超細晶管材步驟如下:第一步:安裝好成形模具,打開冷卻系統。第二步:打開壓縮-擴展擠壓筒加熱裝置,將擠壓筒溫度加熱到300℃;第三步:將Al-0.5Sc合金放入擠壓筒,300℃保溫10min;第四步:開動旋轉擠壓機,擠壓速度為5mm/min;第五步:對制備的制品進行冷卻,冷卻水流量為15L/min。利用該裝置制備的超細晶合金管材組織性能優良。上面結合附圖對本發明的實施例作了詳細說明,但是本發明并不限于上述實施例,在本領域普通技術人員所具備的知識范圍內,還可以在不脫離本發明宗旨的前提下作出各種變化。