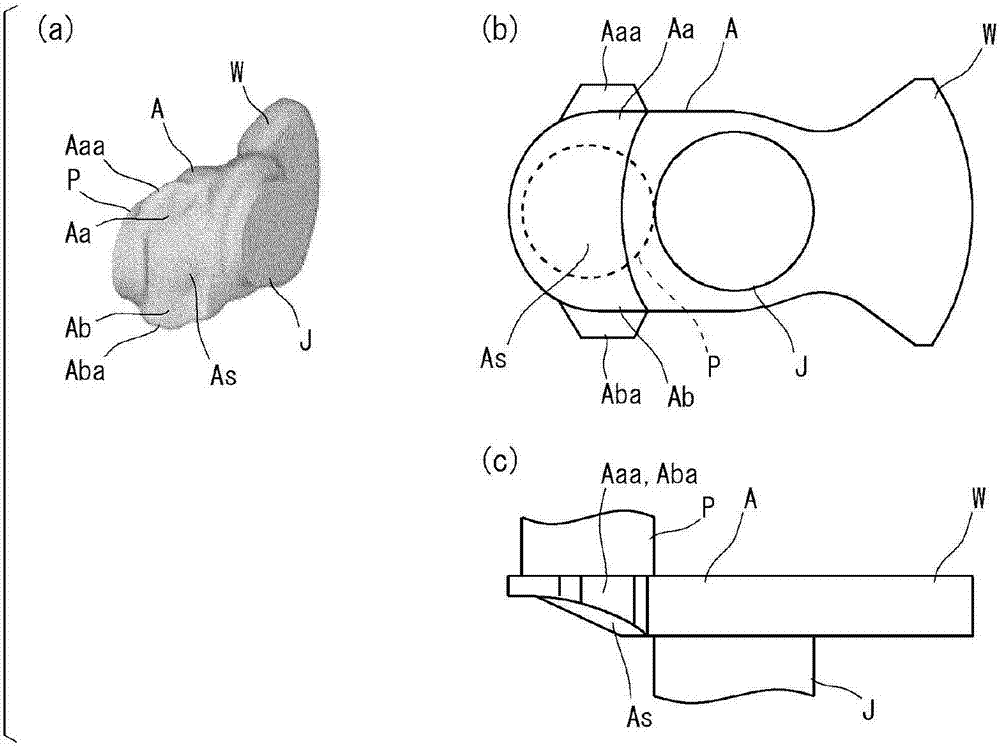
本發明涉及通過熱鍛制造曲軸的方法。
背景技術:汽車、自動兩輪車、農業機械、船舶等的往復式發動機為了將活塞的往復運動變換成旋轉運動而取出動力,曲軸是不可缺少的。曲軸被大致分成通過模鍛制造的曲軸和通過鑄造制造的曲軸。尤其是,在要求高強度和高剛度的情況下,大多使用它們中的特性優異的前者的鍛造曲軸。一般來說,鍛造曲軸以截面為圓形或方形且截面積在整個長度上恒定的鋼坯為原材料,依次經由預成型、模鍛、去飛邊以及整形各工序而制造出來。通常,預成型工序包括輥軋成型和彎曲鍛造各工序,模鍛工序包括粗鍛和精鍛各工序。圖1是用于說明以往的一般的鍛造曲軸的制造工序的示意圖。圖1所例示的曲軸1(參照圖1的(f))搭載于四缸發動機,包括5個軸頸部J1~J5、4個銷部P1~P4、前部Fr、凸緣部FI以及分別將軸頸部J1~J5和銷部P1~P4相連的8個曲軸臂部(以下也簡稱為“臂部”)A1~A8。該曲軸1在全部8個臂部A1~A8一體地具有配重部(日文:カウンターウエイト部)(以下也簡稱為“配重部(日文:ウエイト部)”)W1~W8,曲軸1被稱為四缸-八配重曲軸。以下,在分別統稱軸頸部J1~J5、銷部P1~P4、臂部A1~A8以及配重部W1~W8時,軸頸部的附圖標記也記為“J”,銷部的附圖標記也記為“P”,臂部的附圖標記也記為“A”,配重部的附圖標記也記為“W”。將銷部P以及與該銷部P相連的一組臂部A(包括配重部W在內)也統稱為“曲拐(日文:スロー)”。在圖1所示的制造方法中,如以下那樣制造鍛造曲軸1。首先,在利用感應加熱爐、氣氛加熱爐將預先切斷成預定的長度的圖1的(a)所示的鋼坯2加熱了之后,進行輥軋成型。在輥軋成型工序中,在例如利用孔型輥軋對鋼坯2進行減徑軋制的同時使其體積沿著長度方向分配,成型為作為中間坯料的輥軋鍛坯3(參照圖1的(b))。接著,在彎曲鍛造工序中,從與長度方向成直角的方向將通過輥軋成型而獲得的輥軋鍛坯3局部地加壓壓下,對其體積進行分配,成型為作為更進一步的中間坯料的彎曲鍛坯4(參照圖1的(c))。接下來,在粗鍛工序中,上下使用一對模具對通過彎曲鍛造而獲得的彎曲鍛坯4進行加壓鍛造,成型為造型出曲軸(最終產品)的大致形狀的鍛造件5(參照圖1的(d))。而且,在精鍛工序中,提供通過粗鍛而獲得的粗鍛件5,上下使用一對模具對粗鍛件5進行加壓鍛造,成型為造型出與最終產品的曲軸吻合的形狀的鍛造件6(參照圖1的(e))。在進行這些粗鍛以及精鍛時,多余材料從彼此相對的模具的分模面之間作為飛邊流出。因此,粗鍛件5、精鍛件6在造型出的曲軸的周圍分別帶有較大的飛邊5a、6a。在去飛邊工序中,從上下利用模具保持通過精鍛而獲得的帶飛邊6a的精鍛件6,同時利用刀模將飛邊6a沖裁去除。由此,如圖1的(f)所示,獲得鍛造曲軸1。在整形工序中,從上下利用模具對去除飛邊后的鍛造曲軸1的主要部位、例如、軸頸部J、銷部P、前部Fr、凸緣部FI等這樣的軸部、進而臂部A以及配重部W稍微進行加壓壓下,矯正成最終產品的尺寸形狀。如此一來,制造出鍛造曲軸1。圖1所示的制造工序并不限于例示的四缸-八配重曲軸,即使是在八個臂部A中一部分的臂部具有配重部W的曲軸也是同樣的。在搭載于例如四缸發動機的曲軸中,有時在前頭的第1臂部A1、最后的第8臂部A8以及中央的第4臂部A4、第5臂部A5這兩個臂部設置配重部W。該曲軸被稱為四缸-四配重曲軸。除此之外,即使是搭載于三缸發動機、直列六缸發動機、V型六缸發動機、八缸發動機等的曲軸,制造工序也是同樣的。此外,在需要調整銷部的配置角度的情況下,在去飛邊工序之后追加扭轉工序。近年來,特別是對于汽車用的往復式發動機為了提高燃料經濟性而要求輕量化。因此,作為往復式發動機的主要零件的曲軸,輕量化的要求也愈發顯著。作為謀求鍛造曲軸的輕量化的現有技術,存在下述技術。在日本特開2012-7726號公報(專利文獻1)以及日本特開2010-230027號公報(專利文獻2)中記載有如下臂部:在臂部的軸頸部側的表面上的、將軸頸部的軸心和銷部的軸心連結的直線(以下也稱為“臂部中心線”)上形成有朝向銷部大且深地凹陷的孔部,也記載有具有該臂部的曲軸的制造方法。這些專利文獻1以及2所記載的臂部被輕量化與孔部的體積相應的量。臂部的輕量化導致與臂部成對的配重部的重量減輕,進而導致鍛造曲軸整體的輕量化。另外,這些專利文獻1以及2所公開的臂部在將臂部中心線夾在之間的銷部附近的兩側部使厚度維持得較厚,因此,也確保了剛度(扭轉剛度以及彎曲剛度)。如此,只要將臂部的兩側部的厚度維持得較厚且使臂部的軸頸部側的表面帶有凹坑,就能夠同時謀求輕量化和確保剛度。不過,具有那樣的獨特形狀的臂部的鍛造曲軸難以通過以往的制造方法制造。其原因在于,在模鍛工序中,如果想要在臂部表面形成凹坑,則該凹坑部位的模具的起模斜度成為反斜度,發生成型出的鍛造件無法從模具拔出的事態。為了應對那樣的事態,專利文獻1以及2所記載的制造方法在模鍛工序中不在臂部表面形成凹坑而將臂部成型得較小,在去飛邊工序之后將沖頭壓入臂部的表面,利用該沖頭的痕跡形成凹坑。現有技術文獻專利文獻專利文獻1:日本特開2012-7726號公報專利文獻2:日本特開2010-230027號公報
技術實現要素:發明要解決的問題根據所述專利文獻1以及2所記載的制造方法,能夠將臂部的兩側部的厚度維持得較厚且在臂部的軸頸部側的表面形成凹坑,能夠制造同時謀求了輕量化和確保剛度的鍛造曲軸。不過,在該制造方法中,為了在臂部表面形成凹坑,將沖頭強力地壓入臂部表面而使臂部整體變形,因此,沖頭的壓入需要很大的力。因此,需要用于對沖頭賦予很大的力的特別的設備結構,也需要考慮沖頭的耐久性。本發明的目的在于提供能夠簡便地獲得同時謀求了輕量化和確保剛度的鍛造曲軸的鍛造曲軸的制造方法。用于解決問題的方案本發明的技術方案的鍛造曲軸的制造方法是如下鍛造曲軸的制造方法,該鍛造曲軸具有:作為旋轉中心的軸頸部;相對于該軸頸部偏心了的銷部;以及將所述軸頸部和所述銷部相連的曲軸臂部。該制造方法包括模鍛工序、去飛邊工序以及余料部(日文:余肉部)壓扁工序。在模鍛工序中,成型為造型出如下曲軸的形狀的帶飛邊的精鍛件進行成型:在所述曲軸臂部的所述銷部附近的兩側部各自的外周具有從該外周突出的余料部。在去飛邊工序中,從通過所述模鍛工序而成型出的所述精鍛件將飛邊去除。在余料部壓扁工序中,通過使用了一對第1模具的加壓壓下,針對通過所述去飛邊工序去除了飛邊而成的曲軸將所述曲軸臂部的所述余料部壓扁。在上述的制造方法中,在所述余料部壓扁工序中,能夠設為通過第2模具壓靠所述曲軸臂部的所述軸頸部側的表面中的至少除了所述兩側部的區域的表面來進行保持的結構。在該結構的情況下,優選的是設為如下結構:在所述余料部壓扁工序中,使所述第2模具向所述第1模具的加壓壓下的方向移動而追隨所述第1模具的加壓壓下,將所述第2模具的壓靠于所述曲軸臂部的位置維持在固定的位置。另外,在上述的制造方法中,能夠設為如下結構:在通過使用了模具的加壓壓下來矯正曲軸的形狀的整形工序中實施所述余料部壓扁工序。另外,在上述的制造方法中,在所述余料部壓扁工序中,能夠從與所述銷部的偏心方向成直角的方向實施使用了一對所述第1模具的加壓壓下。另外,在上述的制造方法中,在所述余料部壓扁工...