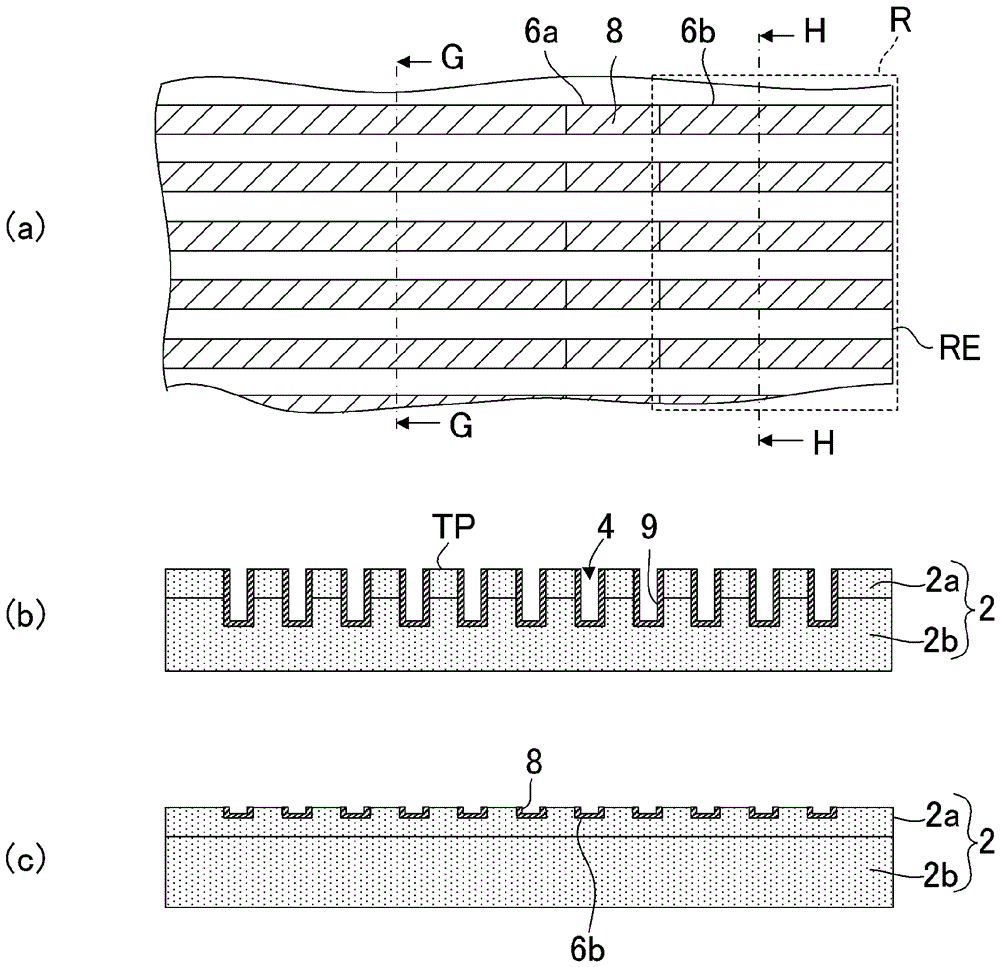
本發明涉及吐出液滴而在被記錄介質進行記錄的液體噴射頭的制造方法、液體噴射頭以及液體噴射裝置。
背景技術:近年來,將墨滴吐出至記錄紙等而記錄字符或圖形,或者將液體材料吐出至元件基板的表面而形成功能性薄膜的噴墨方式的液體噴射頭得到利用。該方式將墨或液體材料(以下,稱為液體)從液體罐經由供給管引導至通道,對填充于通道的液體施加壓力而將液體從與通道連通的噴嘴吐出。在吐出液體時,使液體噴射頭或被記錄介質移動而記錄字符或圖形,或者形成既定形狀的功能性薄膜。作為這種液體噴射頭,已知剪切模式型。剪切模式型的液體噴射頭在沿相對表面垂直的方向實施極化處理的壓電性材料基板的表面形成多個并列的槽,沿鄰接的槽之間的側壁的厚度方向施加電場而使側壁發生厚度滑移變形,從而對填充于槽的液體施加壓力,將液滴從與槽連通的噴嘴吐出。近年來,伴隨著記錄點的高密度化的要求,槽的窄間距化、電極圖案的細微化不斷取得進展。在專利文獻1中,記載有在壓電性材料基板形成多個槽,并通過非電解鍍敷法形成導電膜而制造液體噴射頭的制造方法。首先,利用粘接劑將沿基板表面的垂直方向實施極化處理的2塊壓電性材料基板,極化方向彼此相反朝向地粘合。接著,利用液體抗蝕劑或干膜覆蓋在壓電性材料基板的上表面整個面并固化。接著,使用切割刀片形成槽寬為70μm、深度為300μm的平行的多列槽。接著,實施親水化處理以改良壓電性材料基板的表面,接著進行鍍敷預處理使鍍敷催化劑附著于壓電性材料基板的整個面。接著,通過非電解鍍敷法形成鍍敷膜。接著,通過除去抗蝕劑膜(或干膜)的剝離法從驅動壁的上表面除去抗蝕劑膜(或干膜)和鍍敷膜。圖22是上述處理后的壓電性材料基板101的立體圖(專利文獻1的圖7)。在壓電性材料基板101形成有包含多個平行的槽的通道部102。各通道部102由驅動壁103隔離。通過剝離法除去各驅動壁103的上表面的鍍敷膜120而露出壓電性材料基板101,其他表面被鍍敷膜120覆蓋。接著,使感光性電沉積抗蝕劑附著于壓電性材料基板101而在鍍敷膜120上形成抗蝕劑膜130。接著,通過遮光掩模對形成電極圖案的區域進行遮光,并照射紫外線而曝光。接著,浸漬于顯影液將除去鍍敷膜120的區域的抗蝕劑膜130除去,使鍍敷膜120露出。圖23(a)~(c)表示通過曝光顯影形成抗蝕劑膜130的圖案的壓電性材料基板101的表面(專利文獻1的圖9)。圖23(a)表示壓電性材料基板101的前端面,端面整個面的抗蝕劑膜130通過曝光顯影而被除去,鍍敷膜120露出至整個面。圖23(b)表示壓電性材料基板101的后端面,使各驅動壁103的后端面的鍍敷膜120沿縱向露出。圖23(c)表示壓電性材料基板101的底面,使鍍敷膜120以與露出于后端面的各鍍敷膜120連續的方式露出。接著,進行蝕刻處理除去露出的鍍敷膜120。圖24(a)~(c)表示蝕刻處理后的壓電性材料基板101的表面,分別與圖23(a)~(c)對應。從壓電性材料基板101的前端面除去鍍敷膜120而露出壓電性材料基板101,電極104殘留于驅動壁103的側面(圖24(a))。壓電性材料基板101的后端面形成有通過鍍敷膜120的除去部140而電分離的電極圖案150(圖24(b))。壓電性材料基板101的背面形成有與后端面的電極圖案150電連接的電極圖案150(圖24(c))。接著,在壓電性材料基板101的上表面以閉塞各槽的方式接合未圖示的蓋部件,在壓電性材料基板101的前側的除去鍍敷膜120的表面粘接噴嘴板,并在壓電性材料基板101的底面經由各向異性導電膜接合柔性印刷基板,使柔性印刷基板的布線和底面的各電極圖案150電連接。專利文獻1:日本特開2002-172789號公報。在浸漬于鍍敷液而形成電極的情況下,為了確保壓電性材料基板101與鍍敷膜120之間的密合性,需要在進行鍍敷處理前對壓電性材料基板101的表面進行預處理。然而,抗蝕劑膜沒有對預處理液的耐受性,由于預處理液,抗蝕劑膜130溶解并剝離。因此,如專利文獻1所記載的那樣,難以從驅動壁103的上表面均勻地除去鍍敷膜120。因此,考慮不使用上述那樣的非電解鍍敷法而通過蒸鍍法沉積導電膜,并通過剝離法形成電極圖案。然而,近年來窄間距化得到推進,通道部102的槽寬不斷變窄。在蒸鍍時金屬蒸汽難以進入狹窄的槽寬,因此為了在壁面形成必要厚度的驅動電極需要長時間的蒸鍍。因此,沉積于驅動壁103的上端面的金屬膜變厚,難以通過剝離法除去。另外,在專利文獻1中,在鍍敷膜120上形成抗蝕劑膜130,分別在壓電性材料基板101的后端面和底面設置遮光掩模并進行曝光、顯影,對鍍敷膜120進行蝕刻而形成圖案。因此,制造過程較長,電極圖案的形成需要很多時間。另外,考慮不使用剝離法或光刻及蝕刻法,而通過激光加工形成鍍敷膜120的圖案的方法。然而,在激光加工中必須逐行加工電極圖案,因此電極圖案的形成同樣需要很多時間。
技術實現要素:本發明是鑒于上述課題而做出的,其目的在于,提供不使用抗蝕劑等感光性樹脂而能對金屬膜形成圖案的液體噴射頭及其制造方法。本發明的液體噴射頭的制造方法包括:槽形成工序,在致動器基板的表面的后端附近設定端子區域,沿從所述表面的前端至所述端子區域的方向形成并列的多個吐出槽;淺槽形成工序,在所述端子區域形成淺槽;導電膜形成工序,在所述表面和所述吐出槽及所述淺槽的側面及底面形成導電膜;磨削工序,磨削并除去形成于所述表面的所述導電膜;蓋板接合工序,以使所述端子區域露出并覆蓋所述吐出槽的方式將蓋板接合至所述表面;以及噴嘴板粘接工序,將噴嘴板粘接至所述致動器基板的所述吐出槽開口的側面。另外,所述淺槽形成工序是在所述吐出槽與所述端子區域之間形成與所述吐出槽連續的第一淺槽,并在所述端子區域形成與所述第一淺槽連續的第二淺槽的工序。另外,所述槽形成工序是在鄰接的所述吐出槽之間從所述前端直至所述后端,與所述吐出槽并列地形成虛設槽的工序;所述淺槽形成工序是沿與所述虛設槽交叉的方向形成所述第二淺槽,并且在相對所述第二淺槽而更靠近所述后端的一側,與所述第二淺槽并列地形成第三淺槽的工序;包括:倒角工序,對所述第二淺槽與所述虛設槽交叉的交叉部的所述虛設槽的側面與所述第二淺槽的側面及底面之間的角部進行倒角。另外,包括:背面磨削工序,磨削所述致動器基板的與所述表面相反的一側的背面,除去形成于所述虛設槽的底面的所述導電膜;以及基底基板接合工序,將基底基板接合至所述背面。另外,包括:柔性基板粘接工序,將形成有共用布線和個別布線的柔性基板以使所述共用布線與形成于所述第二淺槽的底面的所述導電膜電連接、使所述個別布線與形成于所述第三淺槽的底面的所述導電膜電連接的方式,粘接至所述端子區域。另外,所述槽形成工序是從所述前端直至所述后端形成吐出槽,并在鄰接的所述吐出槽之間從所述前端直至所述后端,與所述吐出槽并列地形成虛設槽的工序;所述淺槽形成工序是在所述端子區域沿與所述吐出槽交叉的方向形成第二淺槽,并且在相對所述第二淺槽而更靠近所述后端的一側,與所述第二淺槽并列地形成第三淺槽的工序;包括對所述第二淺槽與所述虛設槽交叉的交叉部的所述虛設槽的側面與所述第二淺槽的側面及底面之間的角部、以及所述第三淺槽與所述吐出槽交叉的交叉部的所述吐出槽的側面與所述第三淺槽的側面及底面之間的角部進行倒角的工序。另外,包括:背面磨削工序,磨削所述致動器基板的與所述表面相反的一側的背面,除去形成于所述虛設槽的底面的所述導電膜;以及基底基板接合工序,將基底基板接合至所述背面。另外,包括:柔性基板粘接工序,將形成有共用布線和個別布線的柔性基板以使所述共用布線與形成于所述第二淺槽的底面的所述導電膜電連接、使所述個別布線與形成于所述第三淺槽的底面的所述導電膜電連接的方式,粘接至所述端子區域。另外,所述導電膜形成工序是通過鍍敷法形成所述導電膜的工序。本發明的液體噴射頭包括:致動器基板,在表面的后端附近設定有端子區域,從所述表面的前端朝向所述端子區域的方向形成有并列的多個吐出槽,并在所述吐出槽的側面形成有驅動電極;蓋板,以覆蓋所述吐出槽并使所述端子區域露出的方式,接合于所述致動器基板的所述表面;噴嘴板,粘接于所述致動器基板的所述吐出槽開口的側面;柔性基板,具有布線電極,并粘接于所述端子區域。在所述吐出槽與所述端子區域之間的所述表面形成有第一淺槽,在所述端子區域形成有與所述第一淺槽深度不同的第二淺槽,在所述第一及所述第二淺槽的側面和底面形成有與所述驅動電極電連接的導電膜,所述導電膜與所述布線電極電連接。另外,包括:致動器基板,在表面的后端附近設定有端子區域,從所述表面的前端朝向所述端子區域的方向形成有并列的多個吐出槽,在鄰接的所述吐出槽之間從所述前端直至所述后端,與所述吐出槽并列地形成有虛設槽,并在所述吐出槽及所述虛設槽各自的側面形成有驅動電極;基底基板,接合于所述致動器基板的與所述蓋板相反的一側的背面;蓋板,以覆蓋所述吐出槽并使所述端子區域露出的方式,接合于所述致動器基板的所述表面;噴嘴板,粘接于所述致動器基板的所述吐出槽開口的側面;柔性基板,具有布線電極,并粘接于所述端子區域。在所述端子區域形成有淺槽,在所述淺槽的側面和底面形成有與所述驅動電極電連接的導電膜,所述導電膜與所述布線電極電連接。另外,所述基底基板露出至所述虛設槽的底面。另外,在所述吐出槽與所述端子區域之間的所述表面形成有第一淺槽,在所述端子區域,與所述第一淺槽連續地形成有所述淺槽所包含的第二淺槽。另外,所述淺槽包含第三淺槽,所述第二淺槽沿與所述虛設槽交叉的方向形成,所述第三淺槽與所述第二淺槽并列地形成于相對所述第二淺槽而更靠近所述后端的一側,對所述第二淺槽與所述虛設槽交叉的交叉部的所述虛設槽的側面與所述第二淺槽的側面及底面的角部,進行倒角而除去所述導電膜。另外,所述布線電極包括共用布線和個別布線,形成于所述第二淺槽的底面的所述導電膜與所述共用布線電連接,形成于所述第三淺槽的底面的所述導電膜與所述個別布線電連接。另外,所述淺槽包含第二淺槽和第三淺槽,所述吐出槽從所述前端形成至所述后端,所述第二淺槽沿與所述吐出槽交叉的方向形成,所述第三淺槽與所述第二淺槽并列地形成于相對所述第二淺槽而更靠近所述后端的一側,對所述第二淺槽與所述虛設槽交叉的交叉部的所述虛設槽的側面與所述第二淺槽的側面及底面之間的角部、以及所述第三淺槽與所述吐出槽交叉的交叉部的所述吐出槽的側面與所述第三淺槽的側面及底面之間的角部進行倒角而除去所述導電膜。另外,所述布線電極包括共用布線和個別布線,形成于所述第二淺槽的底面的所述導電膜與所述共用布線電連接,形成于所述第三淺槽的底面的所述導電膜與所述個別布線電連接。本發明的液體噴射裝置包括:上述液體噴射頭;移動機構,使所述液體噴射頭往復移動;液體供給管,將液體供給至所述液體噴射頭;以及液體罐,將所述液體供給至所述液體供給管。本發明的液體噴射頭的制造方法包括:槽形成工序,在致動器基板的表面的后端附近設定端子區域,沿從表面的前端至端子區域的方向形成并列的多個吐出槽;淺槽形成工序,在端子區域形成淺槽;導電膜形成工序,在表面和吐出槽及淺槽的側面及底面形成導電膜;磨削工序,磨削并除去形成于表面的導電膜;蓋板接合工序,以使端子區域露出并覆蓋吐出槽的方式,將蓋板接合至表面;以及噴嘴板粘接工序,將噴嘴板粘接至致動器基板的吐出槽開口的側面。總之,由于通過磨削法將導電膜加工成電極圖案,能夠通過制造工時較少的簡便的方法制造液體噴射頭。附圖說明圖1是本發明的第一實施方式所涉及的液體噴射頭的說明圖;圖2是表示本發明的第一實施方式所涉及的液體噴射頭的制造方法的工序圖;圖3是用于說明本發明的第一實施方式所涉及的液體噴射頭的各制造工序的圖;圖4是用于說明本發明的第一實施方式所涉及的液體噴射頭的各制造工序的圖;圖5是用于說明本發明的第一實施方式所涉及的液體噴射頭的各制造工序的圖;圖6是用于說明本發明的第一實施方式所涉及的液體噴射頭的各制造工序的圖;圖7是用于說明本發明的第一實施方式所涉及的液體噴射頭的各制造工序的圖;圖8是本發明的第二實施方式所涉及的液體噴射頭的說明圖;圖9是表示本發明的第二實施方式所涉及的液體噴射頭的制造方法的工序圖;圖10是用于說明本發明的第二實施方式所涉及的液體噴射頭的各制造工序的圖;圖11是用于說明本發明的第二實施方式所涉及的液體噴射頭的各制造工序的圖;圖12是用于說明本發明的第二實施方式所涉及的液體噴射頭的各制造工序的圖;圖13是用于說明本發明的第二實施方式所涉及的液體噴射頭的各制造工序的圖;圖14是用于說明本發明的第二實施方式所涉及的液體噴射頭的各制造工序的圖;圖15是用于說明本發明的第二實施方式所涉及的液體噴射頭的各制造工序的圖;圖16是用于說明本發明的第二實施方式所涉及的液體噴射頭的各制造工序的圖;圖17是用于說明本發明的第二實施方式所涉及的液體噴射頭的各制造工序的圖;圖18是本發明的第三實施方式所涉及的液體噴射頭的截面示意圖;圖19是本發明的第三實施方式所涉及的液體噴射頭的磨削工序之后的致動器基板的示意性的立體圖;圖20是本發明的第三實施方式所涉及的液體噴射頭的倒角工序之后的致動器基板的示意性的立體圖;圖21是本發明的第四實施方式所涉及的液體噴射裝置的示意性的立體圖;圖22是現有公知的通過剝離法將鍍敷膜從驅動壁的上表面除去的壓電性材料基板的立體圖;圖23表示現有公知的對抗蝕劑膜進行構圖的壓電性材料基板的表面;圖24表示現有公知的蝕刻處理后的壓電性材料基板的表面。附圖標記說明1液體噴射頭;2致動器基板;2a、2b壓電體基板;4吐出槽;5虛設槽;6淺槽、6a第一淺槽、6b第二淺槽、6c第三淺槽;8導電膜;9、9a、9b驅動電極;10蓋板;11液體供給室;12噴嘴板;13噴嘴;14基底基板;15柔性基板;16布線電極、17共用布線、18個別布線;19、19a、19b側壁;20狹縫;21倒角部;23密封材料;24通道;TP表面、BP背面、FE前端、RE后端;R端子區域。具體實施方式(第一實施方式)圖1~圖7是用于說明本發明的第一實施方式所涉及的液體噴射頭及其制造方法的圖。圖1是液體噴射頭1的說明圖,圖2是表示液體噴射頭1的制造方法的工序圖,圖3~圖7是用于說明液體噴射頭1的各制造工序的圖。圖1(a)是液體噴射頭1的示意性的分解立體圖。圖1(b)是AA部分的截面示意圖,圖1(c)是BB部分的截面示意圖的一部分,各自是從箭頭方向觀察的圖。如圖1所示,液體噴射頭1包括:致動器基板2,包含壓電體材料;蓋板10,接合于致動器基板2的表面TP;噴嘴板12,粘接于致動器基板2及蓋板10的前端FE;以及柔性基板15,粘接于在致動器基板2的表面TP的后端RE附近設定的端子區域R。致動器基板2具有層疊沿相對基板面垂直的方向極化、極化方向為彼此相反方向的2塊壓電體基板的構造。致動器基板2在表面TP的后端RE附近設定有端子區域,沿從表面TP的前端FE至端子區域R的方向形成有并列的多個吐出槽4,在該吐出槽4的側面形成有驅動電極9。蓋板10以覆蓋多個吐出槽4并使端子區域R露出的方式接合于致動器基板2的表面TP。由蓋板10閉塞吐出槽4的上部開口而構成通道24。在蓋板10的后側形成有液體供給室11,液體供給室11與各通道24連通并能進行液體的供給。噴嘴板12粘接于致動器基板2的吐出槽4開口的側面。噴嘴13形成于噴嘴板12,并與在致動器基板2的側面開口的吐出槽4(通道24)連通。如圖1(b)及(c)所示,吐出槽4以一定的深度從前端FE形成至中間,從中間開始逐漸變淺地形成。從吐出槽4的后端RE側的端部至端子區域R之間形成有與吐出槽4連續的第一淺槽6a。而且,在端子區域R形成有第一淺槽6a和與第一淺槽6a深度不同的第二淺槽6b。在第一淺槽6a及第二淺槽6b的側面及底面形成有導電膜8,形成于吐出槽4的側面的驅動電極9與形成于吐出槽4的底面的導電膜8連續并電連接。在柔性基板15的致動器基板2側,在與各第二淺槽6b對應的位置形成有布線電極16。柔性基板15經由未圖示的各向異性導電膜粘接于端子區域R。由此,布線電極16經由第一及第二淺槽6a、6b的導電膜8與驅動電極9電連接。液體噴射頭1被如下地驅動。從未圖示的液體罐供給的液體供給至液體供給室11,進一步供給至各吐出槽4。當驅動信號從柔性基板15的布線電極16傳遞至驅動電極9時,吐出槽4的兩側的側壁19發生厚度滑移變形,兩個側壁19所夾著的通道24的容積瞬間增大,接著縮小。由此,液體從液體供給室11引入至通道24,并作為液滴從噴嘴13吐出。圖1所示的情況是通過3周期驅動(3サイクル駆動)從各吐出槽4依次吐出液滴。在此,致動器基板2能夠使用由鈦鋯酸鉛(PZT)構成的壓電陶瓷基板。預先沿相對板面垂直的方向對2塊壓電陶瓷基板實施極化處理,并使極化方向為彼此相反朝向地粘合而形成致動器基板2。通過濺射法、上蒸鍍法或者非電解鍍敷法能夠將導電膜8形成為0.1μm~5μm的厚度。如果通過非電解鍍敷法形成Ni-P,進一步層疊Au,則能夠以低成本且在短時間內形成導電膜8。使用在外周端部埋入金剛石的切割刀片(金剛石砂輪)能夠連續地形成吐出槽4、第一淺槽6a及第二淺槽6b。蓋板10使用線膨脹系數與致動器基板2接近的材料。例如,能夠使用與致動器基板2相同的鈦鋯酸鉛陶瓷。噴嘴板12能夠使用聚酰亞胺薄膜。吐出槽4的深度為300μm~400μm,吐出槽4的寬度及側壁19的厚度為40μm~100μm。第一淺槽6a與第二淺槽6b深度不同。例如,能夠比第二淺槽6b更淺地形成第一淺槽6a。第一淺槽6a通過將蓋板10經由粘接劑接合至其上部而被密封。在該情況下,優選形成于第一淺槽6a的底面的導電膜8的上表面與蓋板10的致動器基板2側的表面之間的間隙較小的方式。這是為了防止供給至吐出槽4的液體滯留于第一淺槽6a。另一方面,柔性基板15能夠通過使布線電極16經由各向異性導電膜嵌合于第二淺槽6b而牢固地粘接。因此,優選比第一淺槽6a更深地形成第二淺槽6b。此外,也能比第二淺槽6b更深地形成第一淺槽6a。在該情況下,在第一淺槽6a與蓋板10之間充分地供給粘接材料,對形成于第一淺槽6a的底面的導電膜8的上表面與蓋板10之間進行密封即可。另外,能夠根據需要在蓋板10的后端與致動器基板2的角部模制密封材料而完全地密封第一淺槽6a。第一淺槽6a及第二淺槽6b具有0.1μm~30μm的深度,并全都具有與吐出槽4相同的槽寬。這樣,在致動器基板2的表面TP的端子區域R形成第二淺槽6b,并在該第二淺槽6b和吐出槽4形成導電膜8即可,因此能夠通過簡便的方法形成液體噴射頭1。使用圖2對本發明的第一實施方式所涉及的液體噴射頭1的制造方法進行說明。如圖2所示,首先,在基板形成工序S0中,形成包含壓電體材料的致動器基板2。接著,在槽形成工序S1中,在致動器基板2的表面TP的后端RE附近設定端子區域R,沿從表面TP的前端FE至端子區域R的方向形成并列的多個吐出槽4。接著,在淺槽形成工序S2中,在致動器基板2的端子區域R形成與吐出槽4連通的第一淺槽6a。接著,在導電膜形成工序S3中,在致動器基板2的表面TP和吐出槽4及第一淺槽6a的側面及底面形成導電膜。此外,如果通過非電解鍍敷法形成導電膜,則能夠以低成本在短時間內形成膜,因此特別地有效。接著,在磨削工序S4中,磨削并除去形成于致動器基板2的表面TP的導電膜8。由此,在致動器基板2的表面TP形成導電圖案。接著,在蓋板接合工序S5中,以使致動器基板2的端子區域R露出并覆蓋吐出槽4的方式,將蓋板10接合至表面TP。接著,在噴嘴板粘接工序S6中,將噴嘴板12粘接至致動器基板2的吐出槽4開口的側面。接著,在柔性基板粘接工序S10中,以使布線電極16與形成于第二淺槽6b的底面的導電膜8電連接的方式將形成有布線電極16的柔性基板15粘接至端子區域R。這樣,在本發明的液體噴射頭1的制造方法中,在致動器基板2的表面形成淺槽,接著在整個面形成導電膜之后,磨削基板表面而留下沉積于淺槽的導電膜的圖案,以此代替在形成導電膜的前后涂敷感光性樹脂,并在形成感光性樹脂的圖案后通過剝離法或者蝕刻法形成導電膜的圖案。因此,能夠圖案形成工時較少地、不需要反復地進行抗蝕劑膜的涂敷、顯影、曝光、蝕刻的復雜的光學加工地形成導電膜的圖案。以下,依據圖3~圖7具體地進行說明。以下,對相同的部分或具有相同功能的部分標記了相同的標號。圖3是用于說明基板形成工序S0的致動器基板2的截面示意圖。在基板形成工序S0中,通過粘接劑使沿與基板表面垂直的方向實施極化處理的壓電體基板2a、以及沿相反方向實施極化處理的壓電體基板2b粘合而形成致動器基板2。比壓電體基板2a更厚地形成壓電體基板2b,在形成吐出槽4時壓電體基板2a與壓電體基板2b的邊界位于槽的深度的中間位置。雖然致動器基板2使用PZT陶瓷,但也能夠使用PZT陶瓷以外的鈦酸鋇等其他壓電體基板。另外,也可以在絕緣體基板上必要的區域形成壓電體基板2a、2b的層疊體作為致動器基板2。圖4是用于說明槽形成工序S1及淺槽形成工序S2的圖,圖4(a)是致動器基板2的局部的平面示意圖,圖4(b)是CC部分的截面示意圖,圖4(c)是DD部分的截面示意圖,圖4(d)是EE部分的截面示意圖。如圖4(a)及(b)所示,在槽形成工序S1中,在致動器基板2的表面TP形成吐出槽4,接著在淺槽形成工序S2中,形成與吐出槽4連續的第一淺槽6a及比第一淺槽6a更深的第二淺槽6b。吐出槽4使用切割刀片從致動器基板2的表面TP的前端FE形成至端子區域R的跟前。切割刀片具有圓盤形狀,因此如圖4(b)所示,吐出槽4的后端RE側的端部成為圓弧形狀。在形成吐出槽4后,使切割刀片上升而形成第一淺槽6a,接著與第一淺槽6a連續地形成第二淺槽6b。由于在之后的磨削工序中將磨削表面TP,吐出槽4以及第一及第二淺槽6a、6b的最終形狀比在槽形成工序S1及淺槽形成工序S2中磨削的深度更淺。因此,優選在淺槽形成工序中比最終形狀更深地形成。吐出槽4形成為深度300μm~400μm,寬度40μm~100μm;第一淺槽6a與吐出槽4連續并形成為深度10μm~40μm,寬度與吐出槽4相同;第二淺槽6b與第一淺槽6a連續并形成為深度30μm~40μm,寬度與第一淺槽6a相同。如圖4(c)所示,構成通道24的區域的吐出槽4具有一定的深度。如圖4(d)所示,形成于端子區域R的第二淺槽6b作為淺槽6形成于壓電體基板2a的表面TP。此外,如已經說明的那樣,可以比第二淺槽6b更深地形成第一淺槽6a,也可以形成為相同的深度。圖5是用于說明導電膜形成工序S3的圖,圖5(a)是致動器基板2的局部的平面示意圖,圖5(b)是FF部分的截面示意圖。在導電膜形成工序S3中,通過非電解鍍敷法在致動器基板2的表面TP和吐出槽4、第一淺槽6a及第二淺槽6b的側面及底面形成導電膜8。首先,對致動器基板2的表面實施鍍敷預處理,接著,通過非電解鍍敷法使Ni-P析出至表面,接著使Au析出而形成由Au和Ni-P構成的導電膜8。導電膜8形成為厚度0.1μm~5μm。通過實施鍍敷預處理能夠提高導電膜8的密封性。圖6是用于說明磨削工序S4的圖,圖6(a)是致動器基板2的局部的平面示意圖,圖6(b)是GG部分的截面示意圖,圖6(c)是HH部分的截面示意圖。如圖6(a)所示,在磨削工序S4中,磨削并除去沉積于致動器基板2的表面TP的導電膜8,在表面TP形成導電膜8的圖案。磨削使用寬度較寬的磨削刀片等,除去導電膜8和表面TP的表層。接著,使用研磨平臺使表面TP平坦化。由此,如圖6(b)及(c)所示,導電膜8殘留于吐出槽4的底面和側面、第一及第二淺槽6a、6b的底面及側面。沉積于吐出槽4的側壁的導電膜8成為驅動電極9。第二淺槽6b的導電膜8作為與外電路的連接用端子起作用。各第二淺槽6b的導電膜8分別與對應的吐出槽4的驅動電極9電連接。圖7(a)是表示在蓋板接合工序S5中,將蓋板10接合至致動器基板2的表面TP的狀態的截面示意圖。蓋板10以使致動器基板2的端子區域R露出并覆蓋吐出槽4的方式,通過粘接劑接合于表面TP。在磨削工序S4中,形成于第一淺槽6a的導電膜8的上端面形成為與表面TP相同程度的高度,因此能夠共面地接合蓋板10和表面TP。即使在蓋板10和表面TP不共面的情況下,由于蓋板10經由粘接劑接合于致動器基板2,也能通過粘接劑密封第一淺槽6a。在蓋板10形成有液體供給室11,液體供給室11與各吐出槽4連通。此外,也能夠在將蓋板10接合至致動器基板2之后,在蓋板10的后端與致動器基板2的角部模制密封材料而完全地密封第一淺槽6a。圖7(b)是表示在噴嘴板粘接工序S6中,通過粘接劑將噴嘴板12粘接至致動器基板2的吐出槽4開口的前端FE的側面的狀態的截面示意圖。在噴嘴板12形成有噴嘴13,噴嘴13與吐出槽4連通。圖7(c)是表示將柔性基板15粘接至致動器基板2的端子區域R的狀態的截面示意圖。在柔性基板15形成有布線電極16,布線電極16與第二淺槽6b的導電膜8經由未圖示的各向異性導電膜電連接。在淺槽形成工序S2中,比導電膜8的厚度和布線電極16的厚度的總計的厚度更淺地形成第二淺槽6b。由此,能夠使導電膜8與布線電極16之間電連接。如上所述,在致動器基板2的表面TP形成第一淺槽6a及第二淺槽6b,通過非電解鍍敷法使導電膜8沉積于該第一及第二淺槽6a、6b,其后,通過除去表面TP的導電膜8形成導電膜8的圖案,因此制造工序較短,并能夠不使用光刻及蝕刻法而簡便地形成電極圖案。此外,雖然在導電膜形成工序S3中通過非電解鍍敷法形成了導電膜8,但本發明不限于此,也可以用濺射法或蒸鍍法代替非電解鍍敷法形成導電膜8。(第二實施方式)圖8~圖17是用于說明本發明的第二實施方式所涉及的液體噴射頭及其制造方法的圖。圖8是液體噴射頭1的說明圖,圖9是表示液體噴射頭1的制造方法的工序圖,圖10~圖17是用于說明液體噴射頭1的各制造工序的圖。對與第一實施方式相同的部分或具有相同功能的部分標記了相同的標號。圖8(a)是液體噴射頭1的示意性的分解立體圖,圖8(b)是沿著吐出槽4的長度方向的截面示意圖,圖8(c)是沿著虛設槽5的長度方向的截面示意圖。如圖8所示,液體噴射頭1包括:致動器基板2,包含壓電體材料;蓋板10,接合于致動器基板2的表面TP;噴嘴板12,粘接于致動器基板2及蓋板10的前方的側面;以及柔性基板15,粘接于致動器基板2的后端RE附近的表面TP的端子區域R。致動器基板2由壓電體材料構成,包括極化方向與基板面垂直并彼此朝向相反方向的2塊壓電體基板2a、2b。在致動器基板2的與蓋板10相反的一側的背面接合有基底基板14。在致動器基板2的表面TP的后端RE附近設定有端子區域R,沿從表面TP的前端FE至端子區域R的方向形成有并列的多個吐出槽4,在鄰接的吐出槽4之間,從前端FE至后端RE,與吐出槽4并列地形成有虛設槽5。在吐出槽4的側面形成有驅動電極9,在吐出槽4的底面形成有導電膜8。在虛設槽5的側面形成有驅動電極9,基底基板14露出至虛設槽5的底面。蓋板10以覆蓋多個吐出槽4及多個虛設槽5并使端子區域R露出的方式,接合于致動器基板2的表面TP。在蓋板10的后側形成有液體供給室11,在液體供給室11中與吐出槽4對應的位置形成有狹縫20。由蓋板10閉塞吐出槽4的上部開口而構成通道24,該通道24經由狹縫20與液體供給室11連通。虛設槽5由蓋板10閉塞上部開口而與液體供給室11不連通。噴嘴板12粘接于致動器基板2及蓋板10的前端FE。噴嘴13形成于噴嘴板12,并與在致動器基板2的前側的側面開口的吐出槽4(通道24)連通。如圖8(b)所示,吐出槽4從致動器基板2的前端FE形成至端子區域R的跟前。吐出槽4的后側的端部具有轉印切割刀片的外形形狀的圓弧形狀。從吐出槽4的后側的端部至端子區域R之間形成有與吐出槽4連續的第一淺槽6a。而且,在端子區域R中,形成有與第一淺槽6a連續并與虛設槽5交叉的第二淺槽6b,在相對第二淺槽6b而更靠近后端RE的一側,與第二淺槽6b并列地形成有第三淺槽6c。比第二及第三淺槽6b、6c深度更淺地形成第一淺槽6a。圖14是表示之后說明的倒角工序后的致動器基板2的局部立體圖,參照該圖14對第一~第三淺槽6a~6c和導電膜8進行說明。在第一~第三淺槽6a~6c的側面及底面形成有導電膜8。形成于第二淺槽6b的底面及側面的導電膜8經由形成于第一淺槽6a的導電膜8與形成于吐出槽4的側面的驅動電極9電連接。形成于第三淺槽6c的導電膜8與形成于虛設槽5的側面的驅動電極9電連接。在此,在第二淺槽6b與虛設槽5交叉的交叉部的虛設槽5的側面與第二淺槽6b的側面及底面的角部形成有倒角部21,導電膜8被除去。其結果是,第二淺槽6b的導電膜8與第三淺槽6c的導電膜8電獨立。如圖8(b)所示,在端子區域R粘接有柔性基板15。在柔性基板15中,與第二淺槽6b對應地形成有共用布線17,與第三淺槽6c對應地形成有個別布線18。柔性基板15經由未圖示的各向異性導電膜粘接于端子區域R。其結果是:第二淺槽6b的底面的導電膜8與吐出槽4的側面的驅動電極9和共用布線17電連接;第三淺槽6c的底面的導電膜8與形成于夾著吐出槽4的2個虛設槽5的吐出槽4側的側面的2個驅動電極9和個別布線18電連接。液體噴射頭1被如下地驅動。從未圖示的液體罐供給的液體供給至液體供給室11,并經由狹縫20填充至各吐出槽4(通道24)。當在柔性基板15的共用布線17與個別布線18之間供給驅動信號時,該驅動信號傳遞至第二淺槽6b的導電膜8和第三淺槽6c的導電膜8。進一步,驅動信號供給至吐出槽4的側面的2個驅動電極9和夾著吐出槽4的2個側壁19的虛設槽5側的驅動電極9,電場沿與側面垂直的方向施加于側壁19a和側壁19b(參照圖14)而發生厚度滑移變形。由此,兩個側壁19a、19b所夾著的吐出槽4(通道24)的容積瞬間增大,接著縮小并從噴嘴13吐出液滴。該情況能夠通過1周期驅動而從各吐出槽4依次吐出液滴。致動器基板2的材料、吐出槽4、第一淺槽6a的深度和寬度、通過非電解鍍敷法的導電膜8的形成、蓋板10及噴嘴板12等與第一實施方式相同,因此省略說明。能夠比吐出槽4和第一淺槽6a寬度更寬地形成第二淺槽6b及第三淺槽6c的寬度。第二及第三淺槽6b、6c的深度可以是20μm~30μm。比導電膜8和共用布線17或個別布線18的總計厚度更淺地形成第二及第三淺槽6b、6c。參照圖9~圖17對本發明的第二實施方式所涉及的液體噴射頭1的制造方法進行說明。圖10是用于說明基板形成工序S0的致動器基板2的截面示意圖。在基板形成工序S0中,經由粘接劑使沿相對基板面垂直的方向實施極化處理、極化方向彼此相反朝向的2塊壓電體基板粘合而形成致動器基板2。比壓電體基板2a更厚地形成壓電體基板2b,之后在形成吐出槽4、虛設槽5時將側壁固定于壓電體基板2b。致動器基板2的材料等與第一實施方式相同,因此省略說明。圖11是用于說明槽形成工序S1和淺槽形成工序S2的說明圖。圖11(a)是致動器基板2的局部平面示意圖,圖11(b)是II部分的截面示意圖,圖11(c)是JJ部分的截面示意圖。在槽形成工序S1中,在致動器基板2的表面TP的后端RE附近設定端子區域R,沿從表面TP的前端RE至端子區域R的方向形成并列的多個吐出槽4直至端子區域R的跟前,并在鄰接的吐出槽4之間,從前端FE至后端RE,與吐出槽4并列地形成虛設槽5。然后,在淺槽形成工序S2中,在吐出槽4與端子區域R之間形成第一淺槽6a,在端子區域R中,沿與第一淺槽6a連續并與虛設槽5交叉的方向形成第二淺槽6b,進一步在相對第二淺槽6b而更靠近后端RE的一側,與第二淺槽6b并列地形成第三淺槽6c。吐出槽4、虛設槽5及第一~第三淺槽6a、6b、6c能夠使用切割刀片磨削而形成。在實際中,連續地形成吐出槽4和與其連續的第一淺槽6a。即,在形成吐出槽4的槽形成工序S1之后,在淺槽形成工序S2中連續地形成與該吐出槽4連續的第一淺槽6a,或以與此相反的順序形成。另外,比吐出槽4更深地形成虛設槽5。吐出槽4形成為深度300μm~400μm,寬度40μm~100μm。由于在之后的磨削工序中將磨削表面TP,吐出槽4、虛設槽5及第一~第三淺槽6a、6b、6c的最終形狀相對在槽形成工序S1及淺槽形成工序S2中磨削的深度變淺。因此,優選在淺槽形成工序中比最終形狀更深地形成。例如,假設在之后的磨削工序中將表面TP磨削約10μm,則第一淺槽6a與吐出槽4連續并形成為深度10μm~40μm,寬度與吐出槽4相同,第二淺槽6b與第一淺槽6a連續并形成為深度30μm~40μm,寬度比第一淺槽6a更寬。能夠以與第二淺槽相同的深度、相同程度的寬度形成第三淺槽6c。虛設槽5形成為與吐出槽4相同程度的寬度或比吐出槽4的寬度更窄,深度比吐出槽4深10μm~100μm。此外,如已經說明的那樣,也可以比第二淺槽6b或第三淺槽6c更深地形成第一淺槽6a,也能形成為相同的深度。圖12是用于說明導電膜形成工序S3的圖。圖12(a)是致動器基板2的局部平面示意圖,圖12(b)是LL部分的截面示意圖。在導電膜形成工序S3中,通過非電解鍍敷法在致動器基板2的表面TP和吐出槽4、虛設槽、第一~第三淺槽6a~6c的底面及側面形成導電膜8。鍍敷預處理、非電解鍍敷法、材料等與第一實施方式相同,因此省略說明。圖13是用于說明磨削工序S4的圖。圖13(a)是致動器基板2的局部平面示意圖,圖13(b)是NN部分的截面示意圖。在磨削工序S4中,磨削并除去形成于致動器基板2的表面TP的導電膜8。磨削使用寬度較寬的磨削刀片等,除去導電膜8和表面TP的表層,并使用研磨平臺使表面TP平坦化。由此,能夠在表面TP附近形成導電膜8的圖案。此外,形成于吐出槽4的側面的導電膜8,即驅動電極9經由第一淺槽6a與第二淺槽6b電連接。另外,形成于虛設槽5的側面的導電膜8,即驅動電極9經由沉積于虛設槽5的側面與第二淺槽6b的底面及側面的角部的導電膜8與吐出槽4的驅動電極9導通。另外,形成于虛設槽5的側面的驅動電極9經由沉積于虛設槽5的側面與第三淺槽6c的底面及側面的角部的導電膜8,與第三淺槽6c的底面的導電膜8導通。因此,在該狀態下吐出槽4的驅動電極9與虛設槽5的驅動電極9電連接。圖14是用于說明倒角工序S7的圖,是致動器基板2的后端RE的局部立體圖。在倒角工序S7中,對第二淺槽6b與虛設槽5交叉的交叉部的虛設槽5的側面與第二淺槽6b的側面及底面之間的角部進行倒角。例如,能夠使用比形成虛設槽5的切割刀片的厚度稍厚的刀片容易地進行倒角。其結果是:虛設槽5的側面的驅動電極9與吐出槽4的側面的驅動電極9電分離;第二淺槽6b的導電膜8和第三淺槽6c的導電膜8作為端子電極起作用。圖15是用于說明蓋板接合工序S5的截面示意圖。在蓋板接合工序S5中,以使端子區域R露出并覆蓋吐出槽4及虛設槽5的方式將蓋板10經由粘接劑接合至表面TP。通過粘接劑密封第一淺槽6a。在蓋板10形成有液體供給室11,液體供給室11與吐出槽4經由狹縫20連通,由蓋板10閉塞虛設槽5的上部開口。其結果是,供給至液體供給室11的液體流入吐出槽4但不流入虛設槽5。圖16是用于說明背面磨削工序S8及基底基板接合工序S9的圖,圖16(a)是背面磨削工序S8之后的截面示意圖,圖16(b)是基底基板接合工序S9之后的截面示意圖。在背面磨削工序S8中,磨削致動器基板2的與表面TP相反的一側的背面BP,除去虛設槽5的底面,留下吐出槽4的底面。由此,形成于虛設槽5的底面的導電膜8被除去,形成于虛設槽5的兩側面的驅動電極9a、9b電分離。接著,在基底基板接合工序S9中,在磨削的背面BP接合基底基板14,閉塞在背面BP開口的虛設槽5。基底基板14使用相對介電常數較小的絕緣體。其結果是:驅動電極9a與驅動電極9b之間的電容耦合比相對介電常數較大的壓電體存在于虛設槽5的底面的情況更小,驅動電極9a與驅動電極9b之間的串擾降低。圖17是用于說明噴嘴板粘接工序S6及柔性基板粘接工序S10的液體噴射頭1的截面示意圖。在噴嘴板粘接工序S6中,將噴嘴板12接合至致動器基板的吐出槽4開口的側面。接著,在柔性基板粘接工序S10中,以使共用布線17與形成于第二淺槽6b的底面的導電膜8電連接,使個別布線18與形成于第三淺槽6c的底面的導電膜8電連接的方式,將形成有共用布線17和個別布線18的柔性基板15粘接至端子區域R。這樣,在通過非電解鍍敷法形成導電膜的前后,不使用感光性樹脂(抗蝕劑膜)、光刻及蝕刻法形成電極圖案,并且通過磨削法成批地分離形成于虛設槽的兩側面的驅動電極,因此能夠通過制造工時較少的簡便的方法制造液體噴射頭。(第三實施方式)圖18是本發明的第三實施方式所涉及的液體噴射頭1的截面示意圖。圖18(a)是吐出槽4的槽方向的截面示意圖,圖18(b)是虛設槽5的槽方向的截面示意圖。與第一及第二實施方式不同的部分是:吐出槽4和虛設槽5從致動器基板2的前端FE形成至后端RE,在蓋板10的后端通過密封材料23密封吐出槽4和虛設槽5。以下,主要對與第二實施方式不同的部分進行說明。對與第一實施方式或第二實施方式相同的部分或具有相同功能的部分標記了相同的標號。在致動器基板的表面TP的后端RE附近構成有端子區域R,從表面TP的未圖示的前端直至后端RE交替并列地形成有吐出槽4和虛設槽5。如圖18(a)所示,在吐出槽4的底部形成有基底基板14和較薄地殘留于基底基板14上的致動器基板2b。在吐出槽4的底面及側面形成有導電膜8及驅動電極9。吐出槽4經由狹縫20與蓋板10的液體供給室11連通,在蓋板10的后端由密封材料23密封。在端子區域R中形成有第二淺槽6b和第三淺槽6c,第二淺槽6b沿與吐出槽4交叉的方向形成,第三淺槽6c在相對第二淺槽6b而更靠近后端RE的一側,與第二淺槽6b并列地形成。形成于吐出槽4的后端RE側的側面的導電膜8與形成于第二淺槽6b的底面及側面的導電膜8電連接。對第三淺槽6c與吐出槽4交叉的交叉部的吐出槽4的側面與第三淺槽6c的側面及底面之間的角部進行倒角而形成倒角部21b。從而使形成于吐出槽4的側面的導電膜8與形成于第三淺槽6c的底面和側面的導電膜8電分離。如圖18(b)所示,在未圖示的致動器基板2的與蓋板10相反的一側的背面接合有基底基板14,基底基板14露出至虛設槽5的底部。在虛設槽5的側面形成有導電膜8及驅動電極9。虛設槽5與蓋板10的液體供給室11不連通,在蓋板10的后端由密封材料23密封。形成于虛設槽5的后端RE側的側面的導電膜8與形成于第三淺槽6c的底面及側面導電膜8電連接。對第二淺槽6b與虛設槽5交叉的交叉部的虛設槽5的側面與第二淺槽6b的側面及底面之間的角部進行倒角而形成倒角部21a。從而使形成于虛設槽5的側面的導電膜8與形成于第二淺槽6b的底面和側面的導電膜8電分離。圖20是此后說明的液體噴射頭1的制造方法中的倒角工序之后的致動器基板2的立體圖,參照該圖對第二淺槽6b及第三淺槽6c進行說明。在致動器基板2的表面交替地形成有吐出槽4和虛設槽5。而且,在第二淺槽6b與虛設槽5交叉的交叉部的虛設槽5的側面與第二淺槽6b的側面及底面之間的角部形成有倒角部21a。同樣地,在第三淺槽6c與吐出槽4交叉的交叉部的吐出槽4的側面與第三淺槽6c的側面及底面之間的角部形成有倒角部21b。倒角部21a的導電膜8被除去,使虛設槽5的側面的驅動電極9與第二淺槽6b的底面的導電膜8電分離。另外,倒角部21b的導電膜8被除去,使吐出槽4的側面的驅動電極9與第三淺槽6c的底面的導電膜8電分離。由此,形成于吐出槽4的側面的驅動電極9與形成于虛設槽5的側面的驅動電極9電分離。再次返回圖18,在端子區域R粘接有包括共用布線17和個別布線18的柔性基板15。柔性基板15的共用布線17經由未圖示的各向異性導電膜與第二淺槽6b的導電膜8電連接,個別布線18經由未圖示的各向異性導電膜與第三淺槽6c的導電膜8電連接。其他結構與第二實施方式相同。第三實施方式所涉及的液體噴射頭1的制造方法基本上與第二實施方式所涉及的液體噴射頭1的制造方法相同,以下,對不同點進行說明。在槽形成工序S1中,從致動器基板2的表面TP的前端FE至后端RE形成吐出槽4,并在鄰接的吐出槽4之間,從前端FE至后端RE,與吐出槽4并列地形成虛設槽5。在該情況下,與第二實施方式同樣地,比吐出槽4更深地形成虛設槽5。接著,進行淺槽形成工序S2、導電膜形成工序S3及磨削工序S4,這些工序與第二實施方式相同,因此省略說明。圖19是本發明的第三實施方式所涉及的液體噴射頭1的磨削工序S4之后的致動器基板2的示意性的立體圖。如圖所示,吐出槽4和虛設槽5從前端FE形成至后端RE,在端子區域R沿與吐出槽4及虛設槽5交叉的方向形成有第二淺槽6b和第三淺槽6c。在吐出槽4、虛設槽5、第二淺槽6b及第三淺槽6c的側面及底面形成有導電膜8。接著,如圖20所示,在倒角工序S7中,對第二淺槽6b與虛設槽5交叉的交叉部的虛設槽5的側面與第二淺槽6b的側面及底面之間的角部進行倒角而形成倒角部21a,使虛設槽5的驅動電極9與第二淺槽6b的底面的導電膜8電分離。另外,對第三淺槽6c與吐出槽4交叉的交叉部的吐出槽4的側面與第三淺槽6c的側面及底面之間的角部進行倒角而形成倒角部21b,使吐出槽4與第三淺槽6c的底面的導電膜8電分離。接著,進行蓋板接合工序S5、背面磨削工序S8、基底基板接合工序S9、噴嘴板粘接工序S6及柔性基板粘接工序S10。這些工序與第二實施方式相同,因此省略說明。此外,通過未圖示的密封材料23密封吐出槽4的后側的開口。這樣,由于從前端FE至后端RE筆直地形成吐出槽4和虛設槽5,在吐出槽4中沒有轉印切割刀片的外形的區域,能大幅度地縮短前端FE與后端RE之間的長度,從而能夠使液體噴射頭1小型化。另外,如已經說明的那樣,在形成導電膜8的前后不需要形成感光性樹脂膜并進行光刻及蝕刻處理,能夠通過制造工時較少的簡便的方法進行制造。(第四實施方式)圖21是本發明的第四實施方式所涉及的液體噴射裝置50的示意性的立體圖。液體噴射裝置50包括:移動機構40,使液體噴射頭1、1’往復移動;流路部35、35’,將液體供給至液體噴射頭1、1’,并從液體噴射頭1、1’排出液體;液體泵33、33’,將液體供給至流路部35、35’;以及液體罐34、34’。各液體噴射頭1、1’包括多個頭基片,各頭基片包括多個通道,并從與各通道連通的噴嘴吐出液滴。液體噴射頭1、1’使用已經說明的第一~第三實施方式的任一個。液體噴射裝置50包括:一對輸送單元41、42,沿主掃掠方向輸送紙等被記錄介質44;液體噴射頭1、1’,將液體吐出至被記錄介質44;滑架單元43,承載液體噴射頭1、1’;液體泵33、33’,將存積于液體罐34、34’的液體按壓供給至流路部35、35’;以及移動機構40,沿與主掃掠方向正交的副掃掠方向掃掠液體噴射頭1、1’。未圖示的控制部控制并驅動液體噴射頭1、1’、移動機構40、以及輸送單元41、42。一對輸送設備41、42沿副掃掠方向延伸,包括接觸輥面且旋轉的柵格輥(gridroller)和夾送輥(pinchroller)。由未圖示的馬達使柵格輥和夾送輥圍繞軸轉移,將夾入輥間的被記錄介質44沿主掃掠方向輸送。移動機構40包括:一對導軌36、37,沿副掃掠方向延伸;滑架單元43,能沿著一對導軌36、37滑動;無接頭帶38,連結滑架單元43并使其沿副掃掠方向移動;以及馬達39,經由未圖示的滑輪(pulley)使該無接頭帶38旋轉。滑架單元43承載多個液體噴射頭1、1’,吐出例如黃色、品紅、青色(cyan)、黑色的4種液滴。液體罐34、34’存積對應的顏色的液體,并經由液體泵33、33’、流路部35、35’供給至液體噴射頭1、1’。各液體噴射頭1、1’按照驅動信號吐出各色液滴。在使液體從液體噴射頭1、1’吐出的時刻,能夠通過對驅動滑架單元43的馬達39的旋轉及被記錄介質44的輸送速度進行控制,在被記錄介質44上記錄任意的圖案。